
- Kindle Store
- Kindle eBooks
- Professional & Technical
Promotions are applied when you make a purchase
These promotions will be applied to this item:

Download the free Kindle app and start reading Kindle books instantly on your smartphone, tablet or computer – no Kindle device required .
Read instantly on your browser with Kindle for Web.
Using your mobile phone camera, scan the code below and download the Kindle app.

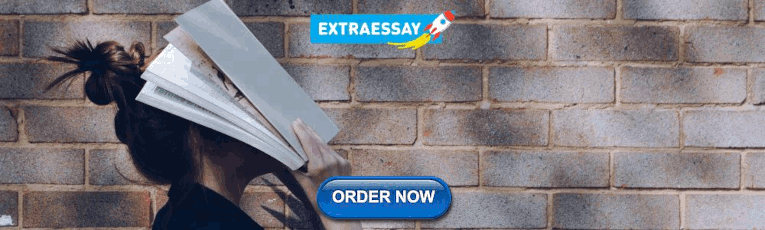
Image Unavailable

- To view this video, download Flash Player
Follow the author

Automotive Manufacturing Processes: A Case Study Approach Kindle Edition
Discusses automotive manufacturing processes in a comprehensive manner with the help of applications. Provides case studies addressing issues in the automotive industry and manufacturing operations in the production of vehicles. Discussion on material properties while laying emphasis on the materials and processing parameters. Covers applications and case studies of the automotive industry.
- Print length 396 pages
- Language English
- Sticky notes On Kindle Scribe
- Publisher CRC Press
- Publication date July 14 2023
- File size 25822 KB
- Page Flip Enabled
- Word Wise Not Enabled
- Enhanced typesetting Enabled
- See all details
Product description
About the author.
Dr. G. K. Awari has done his Ph.D. in Mechanical Engineering and he has more than 30 years of teaching experience at UG/PG/Diploma & Research level and 10 years as an approved Principal of A+ Grade NAAC Accredited Engineering Institute. He is nominated by AICTE as “Margdarshak for NBA Accreditation” of mentee institutes and also working as “Chief Coordinator” of AICTE Mentor institutes for achieving NBA Accreditation to MBI. He has more than 30 Scopus Indexed Journal papers and 10 Patents, 10 Copyrights, to his name. Recently he has been awarded with Patent titled as “HYBRID TOOL CONCEPT FOR BORING, REAMING & CHAMFERING IN A SINGLE TOOL” and Commercial Product is developed for Mahindra and Mahindra, Nagpur. He has been also granted with an Australian Patent on “3D PRINTING of COST EFFECTIVE HUMAN SKULL MODELS AND SKULL INPLANTS”. He has executed more than 8 funded projects of AICTE as a Principal Investigator and organised 10 AICTE-ISTE-SRM University funded National Workshops and 10 International Conferences as a convener. Total grants received for his projects are Rs. 1.14 Crore. He has contributed in the development Academics/Curriculum as Board of Study (BOS) Member at Goa University, Sant Gadgeba Amravati University, YCCE, Nagpur (An Autonomous Institute) and RTM Nagpur University. He is presently BOS member in GH Raisoni University, Saikheda, MP, Delhi Skill and Entrepreneurship University (DSEU), New Delhi and Chairman BOS, Automobile Engineering at Government Polytechnic (GP), Nagpur. He has authored total 10 Books in Engineering and Technology domain and following four books are authored for CRC Press, Taylor and Francis Group. 1. Quantitative Techniques in Business, Management and Finance: A Case study approach. 2. Automotive Systems: Principles and Practice. 3. Additive Manufacturing and 3D Printing Technology: Principles and Practice. 4. Ethics in Information Technology Dr. Awari is recognised Research Supervisor at 4 Indian universities. Total 18 (eighteen) research scholars completed PhD in Mechanical Engineering under his supervision from RTM Nagpur University and SG Amravati University. Currently 06 research scholars are pursuing doctoral research work under his supervision. He is also reviewer of various renowned international journals like ASME, ASCE, and Elsevier, Thermal Science. Dr. Awari belives in the Co-learning Process and Participative management and currently he is Head of Automobile Engineering Department at Government Polytechnic, Nagpur.
Prof. V.S.Kumbhar received Bachelor of Engineering and Master of Engineering degree in Automobile engineering from Shivaji University Kolhapur, Maharashtra, India in 2007 and 2013 respectively. He has total 14 years of experiences. (04 years of industrial experience in automobile manufacturing engineering and 10 years of teaching experience at undergraduate level.) He has taught various subjects like Automobile engines, Automobile systems, Automobile Design, Machine design, Strength of materials, Advanced Engines and Automobile Engineering. His area of interest is fuels and combustion, emission control systems. He has more than 11 international journal publications to his credit and authored a book on “Automotive Systems” for CRC Press, Taylor and Francis Group. He has contributed in the development of Academics as Subject expert for Maharashtra State Board of Technical Education, MSBTE, Mumbai and at Government Polytechnic, Nagpur. He had contributed in academics as BOS member of Automobile Engineering at Government Polytechnic (GP), Nagpur. Prof. Kumbhar is pursuing Ph.D. in Mechanical Engineering at GH Raisoni university, Amravati and currently he is working at Automobile Engineering Department of Government Polytechnic, Awsari Khurd.
Dr. R. B. Tirpude received Bachelor of Engineering degree in Mechanical Engineering from RTM Nagpur University, Nagpur, Maharashtra, India in 1998, M.E. degree in CAD/CAM from Sant Gadgebaba Amravati University, Amravati, Maharashtra, India, in 2008 and Ph.D. in Mechanical Engineering in 2022 from RTM Nagpur University, Nagpur. He has done his MBA (operations) from Delhi university Delhi, India, in 2012. He has total 21 years of teaching experience at undergraduate, research level. He has taught various subjects like Computer Aided Drafting, Hydraulics and Pneumatics, Operation research, Fluid Power, Machine Design and Automobile Engineering. His area of interest is emission control system He has total 19 international journal publications, 10 international conference publications and 11 national conference publications and 10 patents to his name. He has also authored a book on “Automotive Systems” for CRC Press, Taylor and Francis Group. He has been honoured with “ISTE Narsee Munji Best Project Award” and “Shastri Gaurav Purskar-2022. He is also a recipient of “Best Teacher Award” from Government polytechnic Nagpur as well as Dr. Babasaheb Ambedkar National Association of Engineers, Nagpur chapter. He has contributed in the development Academics as Board of Study (BOS) member at MSBTE and various Autonomous institutes of Govt. of Maharashtra. He is presently BOS member of Automobile Engineering at Government Polytechnic (GP), Nagpur. He is currently working in Automobile Engineering Department at Government Polytechnic, Nagpur and handling various collaborations of the department with leading automobile manufacturing industries.
Dr. S.W.Rajurkar received Bachelor of Engineering degree from Visvesvaraya Regional College of Engineering, Nagpur (VRCE) now (VNIT), Nagpur University, Nagpur, Maharashtra, India in 1989 and M.E. degree from Thapar University, Patiala, Punjab, India, in 2001, all in Mechanical Engineering. He has done his Ph.D. from Malaviya National Institute of Technology (MNIT), Jaipur, Rajasthan, India, in 2010. He has more than 30 years of teaching experience at Diploma, Undergraduate, Postgraduate and Research level. He has taught various subjects like Metrology & Quality Control, Manufacturing Process, Industrial Management, Refrigeration & Air conditioning, Operation Research, Machine Design, Engineering Drawing and Automobile Engineering. His area of interest is Supply Chain Management & Industrial Engineering. He has 50 citations including total 07 international journal publications, 16 international conference publications and 4 national conference publications and 4 Patents. 03 research scholars have commenced Ph.D. in Mechanical Engineering under his supervision in 2 Indian universities and one research scholar has completed Ph.D. in Mechanical Engineering under his supervision. He is also a recipient of “ISTE Best Polytechnic Teacher Award for Maharashtra & Goa section for the Year 2016”. He has contributed in the development Academics as Board of Governance (BOG) Member at Government College of Engineering, Chandrapur & also worked as Board of Study (BOS) Member at Government Polytechnic, Nagpur. He is also recognised by AICTE as “Margadarshak” for NBA Accreditation” of mentee institutes. He has authored a Book on “Supply Chain Modelling for perishable Food Products” in LAP Lambert Academic publishing. He has also developed videos /e-content modules for the benefit of students/teachers. He has worked as a Resource person for various Faculty Development Program sponsored by DTE, Mumbai, MSBTE, Mumbai on “NBA”, “Implementation of Outcome Based Education” held at GCOE, Chandrapur, Government Polytechnic, Nagpur, Sakoli and Gondia and at many other institutions. He has also delivered invited Expert lecture on “Logistics & Supply Chain Management” at Management Training program for MCVC/ITI Teachers at G.P. Nagpur. He is Presently working at Government College of Engineering, Chandrapur as Associate Professor & Head of Department, Mechanical Engineering Department & Dean (Administration).
Product details
- ASIN : B0C5P192PT
- Publisher : CRC Press; 1st edition (July 14 2023)
- Language : English
- File size : 25822 KB
- Simultaneous device usage : Up to 4 simultaneous devices, per publisher limits
- Text-to-Speech : Enabled
- Enhanced typesetting : Enabled
- X-Ray : Not Enabled
- Word Wise : Not Enabled
- Sticky notes : On Kindle Scribe
- Print length : 396 pages
About the author
Discover more of the author’s books, see similar authors, read author blogs and more
Customer reviews
No customer reviews.
- Amazon and Our Planet
- Investor Relations
- Press Releases
- Amazon Science
- Sell on Amazon
- Supply to Amazon
- Become an Affiliate
- Protect & Build Your Brand
- Sell on Amazon Handmade
- Advertise Your Products
- Independently Publish with Us
- Host an Amazon Hub
- Amazon.ca Rewards Mastercard
- Shop with Points
- Reload Your Balance
- Amazon Currency Converter
- Amazon Cash
- Shipping Rates & Policies
- Amazon Prime
- Returns Are Easy
- Manage your Content and Devices
- Recalls and Product Safety Alerts
- Customer Service
- Conditions of Use
- Privacy Notice
- Interest-Based Ads
- Amazon.com.ca ULC | 40 King Street W 47th Floor, Toronto, Ontario, Canada, M5H 3Y2 |1-877-586-3230

- Kindle Store
- Kindle eBooks
- Engineering & Transportation
Promotions apply when you purchase
These promotions will be applied to this item:
Some promotions may be combined; others are not eligible to be combined with other offers. For details, please see the Terms & Conditions associated with these promotions.
- Highlight, take notes, and search in the book
Buy for others
Buying and sending ebooks to others.
- Select quantity
- Buy and send eBooks
- Recipients can read on any device
These ebooks can only be redeemed by recipients in the US. Redemption links and eBooks cannot be resold.

Download the free Kindle app and start reading Kindle books instantly on your smartphone, tablet, or computer - no Kindle device required .
Read instantly on your browser with Kindle for Web.
Using your mobile phone camera - scan the code below and download the Kindle app.

Image Unavailable

- To view this video download Flash Player
Follow the author

Automotive Manufacturing Processes: A Case Study Approach 1st Edition, Kindle Edition
Discusses automotive manufacturing processes in a comprehensive manner with the help of applications. Provides case studies addressing issues in the automotive industry and manufacturing operations in the production of vehicles. Discussion on material properties while laying emphasis on the materials and processing parameters. Covers applications and case studies of the automotive industry.
- ISBN-13 978-1032312385
- Edition 1st
- Sticky notes On Kindle Scribe
- Publisher CRC Press
- Publication date July 14, 2023
- Language English
- File size 25822 KB
- See all details
- Kindle (5th Generation)
- Kindle Keyboard
- Kindle (2nd Generation)
- Kindle (1st Generation)
- Kindle Paperwhite
- Kindle Paperwhite (5th Generation)
- Kindle Touch
- Kindle Voyage
- Kindle Oasis
- Kindle Scribe (1st Generation)
- Kindle Fire HDX 8.9''
- Kindle Fire HDX
- Kindle Fire HD (3rd Generation)
- Fire HDX 8.9 Tablet
- Fire HD 7 Tablet
- Fire HD 6 Tablet
- Kindle Fire HD 8.9"
- Kindle Fire HD(1st Generation)
- Kindle Fire(2nd Generation)
- Kindle Fire(1st Generation)
- Kindle for Windows 8
- Kindle for Windows Phone
- Kindle for BlackBerry
- Kindle for Android Phones
- Kindle for Android Tablets
- Kindle for iPhone
- Kindle for iPod Touch
- Kindle for iPad
- Kindle for Mac
- Kindle for PC
- Kindle Cloud Reader
Editorial Reviews
About the author.
Dr. G. K. Awari has done his Ph.D. in Mechanical Engineering and he has more than 30 years of teaching experience at UG/PG/Diploma & Research level and 10 years as an approved Principal of A+ Grade NAAC Accredited Engineering Institute. He is nominated by AICTE as “Margdarshak for NBA Accreditation” of mentee institutes and also working as “Chief Coordinator” of AICTE Mentor institutes for achieving NBA Accreditation to MBI. He has more than 30 Scopus Indexed Journal papers and 10 Patents, 10 Copyrights, to his name. Recently he has been awarded with Patent titled as “HYBRID TOOL CONCEPT FOR BORING, REAMING & CHAMFERING IN A SINGLE TOOL” and Commercial Product is developed for Mahindra and Mahindra, Nagpur. He has been also granted with an Australian Patent on “3D PRINTING of COST EFFECTIVE HUMAN SKULL MODELS AND SKULL INPLANTS”. He has executed more than 8 funded projects of AICTE as a Principal Investigator and organised 10 AICTE-ISTE-SRM University funded National Workshops and 10 International Conferences as a convener. Total grants received for his projects are Rs. 1.14 Crore. He has contributed in the development Academics/Curriculum as Board of Study (BOS) Member at Goa University, Sant Gadgeba Amravati University, YCCE, Nagpur (An Autonomous Institute) and RTM Nagpur University. He is presently BOS member in GH Raisoni University, Saikheda, MP, Delhi Skill and Entrepreneurship University (DSEU), New Delhi and Chairman BOS, Automobile Engineering at Government Polytechnic (GP), Nagpur. He has authored total 10 Books in Engineering and Technology domain and following four books are authored for CRC Press, Taylor and Francis Group. 1. Quantitative Techniques in Business, Management and Finance: A Case study approach. 2. Automotive Systems: Principles and Practice. 3. Additive Manufacturing and 3D Printing Technology: Principles and Practice. 4. Ethics in Information Technology Dr. Awari is recognised Research Supervisor at 4 Indian universities. Total 18 (eighteen) research scholars completed PhD in Mechanical Engineering under his supervision from RTM Nagpur University and SG Amravati University. Currently 06 research scholars are pursuing doctoral research work under his supervision. He is also reviewer of various renowned international journals like ASME, ASCE, and Elsevier, Thermal Science. Dr. Awari belives in the Co-learning Process and Participative management and currently he is Head of Automobile Engineering Department at Government Polytechnic, Nagpur.
Prof. V.S.Kumbhar received Bachelor of Engineering and Master of Engineering degree in Automobile engineering from Shivaji University Kolhapur, Maharashtra, India in 2007 and 2013 respectively. He has total 14 years of experiences. (04 years of industrial experience in automobile manufacturing engineering and 10 years of teaching experience at undergraduate level.) He has taught various subjects like Automobile engines, Automobile systems, Automobile Design, Machine design, Strength of materials, Advanced Engines and Automobile Engineering. His area of interest is fuels and combustion, emission control systems. He has more than 11 international journal publications to his credit and authored a book on “Automotive Systems” for CRC Press, Taylor and Francis Group. He has contributed in the development of Academics as Subject expert for Maharashtra State Board of Technical Education, MSBTE, Mumbai and at Government Polytechnic, Nagpur. He had contributed in academics as BOS member of Automobile Engineering at Government Polytechnic (GP), Nagpur. Prof. Kumbhar is pursuing Ph.D. in Mechanical Engineering at GH Raisoni university, Amravati and currently he is working at Automobile Engineering Department of Government Polytechnic, Awsari Khurd.
Dr. R. B. Tirpude received Bachelor of Engineering degree in Mechanical Engineering from RTM Nagpur University, Nagpur, Maharashtra, India in 1998, M.E. degree in CAD/CAM from Sant Gadgebaba Amravati University, Amravati, Maharashtra, India, in 2008 and Ph.D. in Mechanical Engineering in 2022 from RTM Nagpur University, Nagpur. He has done his MBA (operations) from Delhi university Delhi, India, in 2012. He has total 21 years of teaching experience at undergraduate, research level. He has taught various subjects like Computer Aided Drafting, Hydraulics and Pneumatics, Operation research, Fluid Power, Machine Design and Automobile Engineering. His area of interest is emission control system He has total 19 international journal publications, 10 international conference publications and 11 national conference publications and 10 patents to his name. He has also authored a book on “Automotive Systems” for CRC Press, Taylor and Francis Group. He has been honoured with “ISTE Narsee Munji Best Project Award” and “Shastri Gaurav Purskar-2022. He is also a recipient of “Best Teacher Award” from Government polytechnic Nagpur as well as Dr. Babasaheb Ambedkar National Association of Engineers, Nagpur chapter. He has contributed in the development Academics as Board of Study (BOS) member at MSBTE and various Autonomous institutes of Govt. of Maharashtra. He is presently BOS member of Automobile Engineering at Government Polytechnic (GP), Nagpur. He is currently working in Automobile Engineering Department at Government Polytechnic, Nagpur and handling various collaborations of the department with leading automobile manufacturing industries.
Dr. S.W.Rajurkar received Bachelor of Engineering degree from Visvesvaraya Regional College of Engineering, Nagpur (VRCE) now (VNIT), Nagpur University, Nagpur, Maharashtra, India in 1989 and M.E. degree from Thapar University, Patiala, Punjab, India, in 2001, all in Mechanical Engineering. He has done his Ph.D. from Malaviya National Institute of Technology (MNIT), Jaipur, Rajasthan, India, in 2010. He has more than 30 years of teaching experience at Diploma, Undergraduate, Postgraduate and Research level. He has taught various subjects like Metrology & Quality Control, Manufacturing Process, Industrial Management, Refrigeration & Air conditioning, Operation Research, Machine Design, Engineering Drawing and Automobile Engineering. His area of interest is Supply Chain Management & Industrial Engineering. He has 50 citations including total 07 international journal publications, 16 international conference publications and 4 national conference publications and 4 Patents. 03 research scholars have commenced Ph.D. in Mechanical Engineering under his supervision in 2 Indian universities and one research scholar has completed Ph.D. in Mechanical Engineering under his supervision. He is also a recipient of “ISTE Best Polytechnic Teacher Award for Maharashtra & Goa section for the Year 2016”. He has contributed in the development Academics as Board of Governance (BOG) Member at Government College of Engineering, Chandrapur & also worked as Board of Study (BOS) Member at Government Polytechnic, Nagpur. He is also recognised by AICTE as “Margadarshak” for NBA Accreditation” of mentee institutes. He has authored a Book on “Supply Chain Modelling for perishable Food Products” in LAP Lambert Academic publishing. He has also developed videos /e-content modules for the benefit of students/teachers. He has worked as a Resource person for various Faculty Development Program sponsored by DTE, Mumbai, MSBTE, Mumbai on “NBA”, “Implementation of Outcome Based Education” held at GCOE, Chandrapur, Government Polytechnic, Nagpur, Sakoli and Gondia and at many other institutions. He has also delivered invited Expert lecture on “Logistics & Supply Chain Management” at Management Training program for MCVC/ITI Teachers at G.P. Nagpur. He is Presently working at Government College of Engineering, Chandrapur as Associate Professor & Head of Department, Mechanical Engineering Department & Dean (Administration).
Product details
- ASIN : B0C5P192PT
- Publisher : CRC Press; 1st edition (July 14, 2023)
- Publication date : July 14, 2023
- Language : English
- File size : 25822 KB
- Simultaneous device usage : Up to 4 simultaneous devices, per publisher limits
- Text-to-Speech : Enabled
- Enhanced typesetting : Enabled
- X-Ray : Not Enabled
- Word Wise : Not Enabled
- Sticky notes : On Kindle Scribe
- Print length : 424 pages
About the author
Discover more of the author’s books, see similar authors, read author blogs and more
Customer reviews
Customer Reviews, including Product Star Ratings help customers to learn more about the product and decide whether it is the right product for them.
To calculate the overall star rating and percentage breakdown by star, we don’t use a simple average. Instead, our system considers things like how recent a review is and if the reviewer bought the item on Amazon. It also analyzed reviews to verify trustworthiness.
No customer reviews
- Amazon Newsletter
- About Amazon
- Accessibility
- Sustainability
- Press Center
- Investor Relations
- Amazon Devices
- Amazon Science
- Sell on Amazon
- Sell apps on Amazon
- Supply to Amazon
- Protect & Build Your Brand
- Become an Affiliate
- Become a Delivery Driver
- Start a Package Delivery Business
- Advertise Your Products
- Self-Publish with Us
- Become an Amazon Hub Partner
- › See More Ways to Make Money
- Amazon Visa
- Amazon Store Card
- Amazon Secured Card
- Amazon Business Card
- Shop with Points
- Credit Card Marketplace
- Reload Your Balance
- Amazon Currency Converter
- Your Account
- Your Orders
- Shipping Rates & Policies
- Amazon Prime
- Returns & Replacements
- Manage Your Content and Devices
- Recalls and Product Safety Alerts
- Conditions of Use
- Privacy Notice
- Consumer Health Data Privacy Disclosure
- Your Ads Privacy Choices

- Previous Article
- Next Article
1 Motivating the Study on Change Management
2 state of the art of change management, 3 case study, 4 analysis of differences, 5 conclusions, conflict of interest, data availability statement, part change management: a case study on automotive engineering and production; domestic and international perspectives.
- Split-Screen
- Article contents
- Figures & tables
- Supplementary Data
- Peer Review
- Open the PDF for in another window
- Cite Icon Cite
- Permissions
- Search Site
Knackstedt, S., Sutton, M., and Summers, J. D.Part Change Management: A Case Study on Automotive Engineering and Production; Domestic and International Perspectives ASME Open J. Engineering ASME. January 2023 2 021012 doi: https://doi.org/10.1115/1.4056813
Download citation file:
- Ris (Zotero)
- Reference Manager
Due to interest in aspects such as process, strategies, and tools of engineering changes expressed in a literature review, a case study was done on a major automotive original equipment manufacturer (OEM) to assess the perceived quality of its part engineering change management process and supporting system through its employees’ eyes. A combination of 12 interviews lasting 12 h and 46 written surveys was used to capture the views of participants from all major functions found at the research and development (R&D) headquarters of the OEM: Purchasing, Production, Development, and one group consisting of all other functions (“Other”). Statistical analysis was performed to identify statistically significant differences between employee perceptions of an engineering change management system among different departments, amount of use, and years of use. It was found that statistically significant differences exist in terms of understanding the usability of the system between different departments and also between different years of experience.
Changes to parts in the automotive industry come from two sources [ 1 ]: (1) creating innovative features that are implemented in existing vehicles and (2) managing existing features, where innovation is defined as “the multi-stage process whereby organizations transform ideas into new/improved products, service or processes, to advance, compete and differentiate themselves successfully in their marketplace” [ 2 ]. This definition is based on an analysis of word clustering among 60 definitions from 1934 to 2010 [ 2 ]. Managing these changes is increasingly important, not only as the rate of innovation increases [ 1 ] but also as companies continue to seek to improve quality and sustainability while meeting new regulations, often resulting in changes to existing parts [ 3 ]. A consumer survey conducted in 2008 showed that 86% of respondents list quality as the most important factor in buying a new vehicle [ 4 ]. The results of this survey show the importance of quality to the customer, explaining why many companies list quality concerns as a main source for part engineering changes [ 3 , 5 , 6 ]. Furthermore, the implementation of some engineering changes can lead to cost reductions for the company, which can have a significant impact on the company’s financial standing [ 7 ].
1.1 What is Part Engineering Change?.
To understand what is meant by P-EC (part engineering change), it is necessary to understand what is meant by parts in the context of this paper, the kind of changes part engineering change entails, and the sources of these changes. For the purpose of this paper, parts refer to any item that is identified on the Bill of Materials at the original equipment manufacturer (OEM). Additionally, different definitions of the term part engineering change management (P-ECM) exist due to the breadth of work that has been performed on this topic. Here, change is defined as “engineering change orders (ECOs)—changes to parts, drawings or software that have already been released” [ 8 ]. This definition is used in several other research efforts [ 5 , 9 ].
The reasons for engineering part changes can come from a variety of sources [ 3 , 10 ]. At the company that was the focus of this paper, data analysis shows the common sources include quality improvements, cost savings, safety concerns, legal considerations, and ergonomic changes benefitting the employee assembling the vehicle. Examples of each of the aforementioned engineering part change sources can be seen in Table 1 . The exact frequency is withheld here for proprietary reasons.
Examples of engineering part changes
Examination of engineering change data at the automotive OEM showed that in a 20-month period in the middle of a product’s lifecycle, 1211 changes of all kinds were made. Quality and/or product improvement is the most frequent reason for a part engineering change and accounted for over half of the changes. Many changes are also due to cost savings. According to one interviewee, removing a painted component and replacing it with a black component can reduce vehicle costs by almost €1/vehicle. In an industry where some automobile manufacturers produce over 10 million vehicles annually, these savings make a significant difference to the company. These types of changes accounted for approximately a quarter of total changes. Another driver of change is safety concerns. A component will generally be changed as soon as possible if there is a safety concern [ 5 ]. For example, battery connections that can become corroded due to water and/or salt must be redesigned as these corrosions could lead to the loss of electrical power to safety-critical components such as the brakes. These types of changes are rare, but it was not possible to filter the available data for these types of changes. Less common are legal considerations and ergonomic changes. Legal changes can include changes to laws in countries around the world. For example, some Gulf States require a sticker on the vehicle that describes the fuel economy of the vehicle. While this is not strictly a part change because neither the windshield that bears the sticker nor the fuel system itself is affected, it is a change that needs to be made to the final vehicle before it is shipped. These types of changes are rare and account for less than 5% of the changes. To make the assembly of the vehicle more employee-friendly, ergonomic changes can also be made. One example of this is a preassembly of a wiring harness inside the vehicle. By preassembling this harness, only one connection has to be made once the harness has been installed in the vehicle. As these connections are frequently made in tight spaces, reducing the number of occurrences to one helps the associates. These types of changes are rare, but it was not possible to filter the available data for these types of changes
Other industries are also affected by similar sources, albeit not limited to those listed in Table 1 . In the defense industry, the most common sources as determined by an industry roundtable discussion are a change in requirements or regulations, quality/cost/durability, sustainability, product integration, and project management [ 3 ]. Ergonomic changes have been studied to increase employee output, especially in the furniture industry where carpal tunnel syndrome and tendinitis are more prevalent than in other industries [ 11 ]. Furthermore, it has been shown that legal considerations can account for roughly 20% of engineering changes in the civil engineering design community [ 7 , 12 ]. Regardless of industry, the reasoning behind making an engineering change is frequently the same. All changes require some combination of efforts such as time, cost, and risk. By making a change, the company hopes that the positive aspects of the change, such as improved cost or quality outweigh these negative aspects.
Engineering changes and their management (process and tools) in the industry have been reviewed from several different angles, such as time management and financial management [ 12 – 17 ], as well as P-ECM tool use. The process can be highly complex depending on the type of product and industry involved. To help with this complexity, companies have developed numerous in-house tools that track financial and temporal information [ 3 , 16 , 18 , 19 ]. Furthermore, these can be broken down into research regarding strategies, change propagation, process responsibilities, change drivers, other tools and findings as well as process descriptions.
1.2 Research Questions.
How do employees engage with the engineering change management process and tool?
If so, how do these issues align with differences between departments?
To understand the need for ECs and ECM processes, a review of the related literature was conducted. This included definitions of ECs, an explanation of change propagation and the potential impacts of the phenomenon, and trends in ECM research. Additionally, suggestions for improvements in ECM methods were explored. Lastly, a comparison of the different process models used in ECM studies was conducted.
2.1 Engineering Change.
The definition of engineering change differs slightly depending on the perspective of the research being conducted. Raffaeli et al. defined ECs as a series of changes that impact the components of a product after production has begun for that product [ 20 ]. Another study defined EC as an “alteration made to parts, from embodiment design stage through production stage, in its form or fit or function, drawings or software that has already been released” [ 10 , 21 ]. Knackstedt and Summers gave a similar definition in their study of part change management, which said that ECs were changes to parts, drawings, or software that had already been released [ 22 , 23 ]. Additional context for that definition was given, which stated that ECs are typically made for reasons of either quality and product improvement or to increase cost savings. The literature review conducted by Wright defined EC as a modification to a component of a product after the product is in production [ 24 ]. A commonly used explanation of ECs defined the concept as the changes or modifications in the forms, fits, materials, dimensions, or functions of a component after the product design is released [ 19 , 25 , 26 ]. Huang et al. further elaborated on the EC phenomenon, explaining that ECs typically induce a series of downstream changes that flow across companies and require multi-disciplinary teams to address the effects [ 25 ].
Engineering changes can be broken down into two categories: initiated changes and emergent changes [ 27 – 29 ]. Initiated changes stem from a response to altered customer requirements or from internal innovations in design. Some of the driving factors of initiated changes from the outset of a product design include customer requirements, from general capability statistics to specific equipment; certification requirements, including government codes and environmental standards; innovations, in materials or in processes; and problems identified from past designs. Other factors that can introduce initiated changes even later into the product design process involve new customer requirements, such as changing operation environments or marketplaces; recent innovations, which are more common for products with a long design period; and retrofits, common for products with a long life cycle [ 27 ]. Emergent changes are caused in response to problems occurring during the design process, or from weaknesses identified in the product. The aforementioned problems could occur during the initial part design, as some changes cannot be predicted by computer-aided design (CAD) systems, or during testing, prototyping, and manufacturing phases. Additionally, problems occurring during the use of the product could cause emergent changes as issues are addressed [ 27 ].
Traditionally, engineering changes have been considered a hindrance in the design and manufacturing process. In the literature review conducted by Wright, opinions on different aspects of the manufacturing process are presented [ 24 ]. The manufacturing perspective thinks of ECs as an evil that has the potential to disrupt production operations. Production control views ECs as a source of confusion that has the potential to upset a precarious balance of manufacturing resources, while inventory control sees ECs in terms of the cost of the scrap and rework that would potentially be produced. This sentiment is echoed by Huang et al. in their study of the ECM methods employed in Hong Kong manufacturers, as the companies involved found the management of ECs to be costly and time-consuming [ 25 ]. ECs were also found to have a noticeable negative effect on the delivery time of products, as well as less prominent but still adverse effects on product quality, day-to-day jobs, and workmanship. The article written by Jarratt et al. similarly found that ECs were considered to be a major source of problems in the part development process [ 29 ].
Despite these negative perceptions, ECs are increasingly seen as a way to keep up with the market and implement continuous improvement. Raffaeli et al. stated that ECs represent a key aspect of innovation, especially with regards to product families of standard parts or solutions, as ECs allow for more variants to be created in order to satisfy niche market demands [ 30 ]. Huang and Mak found support for that statement, in that companies gain significant market competitiveness if ECs are handled properly [ 19 ]. Similarly, Wright’s review of ECM literature showed that the incremental improvements made to products using ECs lead to vast leaps in innovation, as well as the fact that EC is a key process that allows companies to stay competitive in the market and effective in their product design [ 24 ]. Kidd and Thompson echoed this sentiment and summed up the new viewpoint toward ECs, saying that ECM has a vital role in all successful industrial organizations [ 31 ].
The new view on ECs is timely, as, across manufacturing industries, there has been a widespread shift in the approach to manufacturing, from mass production to mass customization [ 32 ]. This new approach has been embraced by manufacturers because of the need to make continuous improvements in order to create competitive products [ 31 ]. Mass customization is seen as the best way to satisfy individual needs through products while still turning a profit [ 33 ]. However, this approach introduces new issues to the traditional consideration of EC and change propagation. The greater connectivity that is created between systems using a mass customization, modular system architecture, or product family approach leads to a greater probability that changes will spread to other systems [ 27 ]. Eckert et al. also found that complex products with parts or systems that are tightly linked are more susceptible to change propagation [ 27 ]. Building on this, Raffaeli et al. found a need to extend EC methods in a way that allows for the evaluation of the impact that a change to a single product has on the overall product family [ 30 ].
Engineering change as it relates to manufacturing has been studied through mapping to general process models [ 34 ]. For instance, one model views three basic steps of a manufacturing change management process: before approval, during approval, and after approval [ 35 ]. This work was limited to looking at general phases and did not deeply study the roles of individuals, the timing, or the criticality of the proposed changes. An expansion of this included a cyclic model that required the manufacturing engineer to submit a proposal to the engineering team (the owner of the product, often the development team, but not always) that requires approval before implementation. A challenge identified with this approach is that the production is ongoing and that the change is either implemented immediately pending retraction or manufacturing waits for approval. This resulted in iterative revisions to proposals approved [ 36 ]. Another model focuses on identifying the need, selecting the solution, approving the change intent, approving and releasing updated documents, and communicating modifications. Between selecting the solution and approving the change, this process argues for a pause in production (a decrease in work), but additional steps are required between approving the change and releasing approved and updated documents when compared to the traditional process [ 37 ].
The sources for change in manufacturing can be from the production line, from quality control offices, supplier changes, design changes, or logistics modifications [ 10 , 34 ]. An example of design changes may take the form of introduction of new options or packages in a vehicle model. Option change management intersects both manufacturing and design [ 32 ]. While there are some differences between design engineering changes and manufacturing engineering changes, the processes for implementing these are similar. The main distinction tends to be with respect to the authority to implement the change and the timeliness associated with manufacturing changes during production.
2.2 Change Propagation.
The trickle-down nature of change is commonly referred to as change propagation; however, the definition of this term varies between researchers. Shankar et al. considered change propagation as the effects of changes that spread to other design sections [ 21 ]. Another study by Shankar et al. defined change propagation as the phenomenon by which one change sparks a series of other changes, which is typically studied by considering the linking parameters as the root cause of the spread [ 10 ]. Rouibah and Caskey found that stronger couplings between components increase the possibility that changes in one component will cause a change in another part [ 26 ]. An oft-cited explanation of change propagation defines it as the process by which a change to one part of an existing design or system configuration results in additional changes to the system, when those changes would not otherwise have been required [ 27 – 29 ]. Further breakdown of the phenomenon includes the types of behavior exhibited by components in response to a change, as well as the characterization of propagation types. When a change is introduced to a system or environment, components can act as constants, absorbers, multipliers, resistors, or reflectors. Propagation itself can be characterized as change ripples or change blossoms, if the changes finish on time differentiated by the size of the initial change effort, or as change avalanches, if the changes do not finish on time [ 27 – 29 ].
A study by Shankar et al. looked extensively into the reasons for change propagation [ 10 ]. In the study, 77% of all changes were internal changes, with the remaining 23% considered external changes. Internal changes were found to be caused by document error corrections, cost reduction exercises, manufacturing issues, design corrections, and inventory issues. External changes largely stemmed from changes to customer requirements. Further study broke down changes into propagated and initiated changes. The propagated changes were discovered to come from inventory issues, design error rectification, and manufacturing difficulties [ 10 ].
Further studies have explored methods of measuring and capturing trends in change propagation. Raffaeli et al. considered a method to measure the extent of change propagation and the linkages between changes and found that most of the existing work looks at linkages in the physical domain or in the functional domain [ 30 ]. However, few studies look at the connections between the physical and functional domains. With regards to capturing trends, Eckert et al. used a design structure matrix to show the connection network between trends and to look at the relationship between affecting and affected parameters [ 27 ]. Giffin et al. studied a data set of over 41,500 change requests and used graph theory to find change networks [ 28 ]. From this analysis, they found that the large change networks tend to coalesce based on nucleation in different parts of the system. Additionally, Giffin et al. constructed 1-, 2-, and 3-change motifs, which were used to categorize and characterize the trends in the change requests data. This data can then be used to determine a way to manage the extent of the engineering change propagation.
2.3 Engineering Change Management.
Engineering change management is defined as an activity in which the design change life cycle is monitored [ 31 ]. Rouibah and Caskey and Bouikni et al. go further in their definitions, stating that ECM is the process of making ECs in a planned, systematic manner that typically consists of engineering change requests and engineering change orders [ 26 , 38 ]. Many studies discussing ECs and ECM describe the steps for a successful ECM system. Kidd and Thompson mentioned a multi-stage cycle of change proposal, work order, and specific instructions, change implementation, and release approval for the ECM systems they reviewed [ 31 ]. Another procedure, consisting of identification, evaluation, implementation, and audits of ECs, was discussed in the study of ECM in UK manufacturing industries conducted by Huang and Mak [ 19 ]. Rouibah and Caskey posed an ECM system with four key steps: tracking change impact on product structure elements, identifying the people to be informed of the change, determining a sequence for informing the previously identified people, and executing approval and release of workflow with the participation of all involved parties [ 26 ]. A fourth set of steps was posited by Phelan et al. which consisted of the EC request, development of possible solutions, evaluation of change impacts, EC approval, implementation, and then review of the EC [ 32 ].
Although ECM systems are specialized to work with individual companies, there are some general trends. When first introduced, most ECM systems were paper-based and used the highly inefficient strategy of sequential review [ 19 , 25 , 29 , 31 ]. ECM systems then moved to a more computer-aided approach, in which the systems provided electronic documents that functioned in the same manner as traditional paper documents [ 19 , 25 , 26 ]. Once product data management (PDM) systems became available, many companies began integrating the ECM and PDM systems [ 26 , 31 ]. Huang and Mak determined from their research into the practice of ECM that most ECM systems are formally defined, with clear procedures, with most decisions and meetings involving both the design office and the industrial and production department [ 19 ]. Also identified were the barriers to using ECM efficiently: poor communication and late problem discovery, which leads to panicking and easy acceptance of quick fixes.
Across the literature reviewed, a common theme was the need for improvement to the ECM system and process. Thus, many of the reviewed articles discussed systems or tools. Shankar et al. proposed a seven-step verification validation and testing (VV&T) planning and computational tool, designed to guide a change engineer through the process and reduce human error by carrying over information between computational steps [ 21 ]. Rouibah and Caskey suggested a five-step parameter-based model for ECM, distinct from existing process- or document-dependent models, that would support communication in distributed engineering environments across company borders [ 26 ].
Kidd and Thompson discuss the in-house custom-designed software system used at British Aerospace (Military Aircraft Division) (BAe(MAD) and its three key advantages [ 31 ]. The BAe(MAD) system allows customers as well as the design and manufacturing departments to initiate design changes, notifies all affected departments or individuals of the change proposals, and requires those affected to give advice on the design change. The system also locks CAD files and only releases drawings when changes affect them, thus preventing documentation errors [ 31 ].
The study conducted by Huang and Mak on the ECM methods used in manufacturing industries in the UK found both tools and systems in use [ 19 ]. Commonly used systems include computer-aided design (CAD) and manufacturing (CAM) as well as material requirements planning (MRP) software. Many companies were also found to use design tools such as quality function deployment (QFD), failure modes and effects analysis (FMEA), design for manufacturing and assembly (DFM/DFA) principles, and value analysis in order to control ECs.
Bouikni et al. proposed a product feature evolution validation (PFEV) model that would support formal modification processes used for ECM after the initial product release [ 38 ]. The model would create a dynamic workflow that would offer the flexibility to efficiently handle the informal pre-release EC process, in addition to the formal post-release process. This would be done by incorporating the concepts of shared product features between disciplines, introducing an estimator of change, and generation of discipline- and task-specific information sets.
Other proposed models include the meta-product model that addresses both functional and modular part structures and product architectures [ 30 ]. Eckert et al. suggested modeling ECs using a problem-solution-evaluation loop, representing both a forward partial redesign process and a backward debugging process [ 27 ]. Shankar et al. created a model that would translate change interactions to a domain mapping matrix [ 10 ]. Similarly, Jarrett et al. proposed a change prediction method that would combine design structure matrices with risk management techniques [ 29 ].
Given the research questions proposed in the previous section, a case study was used to answer these questions. This section will give details on case studies, and data collection.
3.1 The Case Study Methodology.
A case study is an objective, in-depth look into the uncontrolled environment offered by companies in industry or universities in an academic setting [ 39 , 40 ]. It can be used for different reasons; providing a description, generating a theory, or testing a theory is among the most common [ 41 ].
A case study can focus on just one company or examine multiple companies to compare and contrast a situation. Within one case study, it is also possible to study processes specific to one company or processes that have become common throughout the entire industry [ 42 ]. Case Studies can use multiple research methods, such as interviews, surveys, and experiential analysis to add credibility to the research while helping to ensure the results are valid and accepted [ 39 , 40 , 43 ]. The case study described here used interviewing and a survey to generate data. An interview and survey approach to understanding the change management process for line-sustaining engineering was selected to provide a broader comparative understanding of organizational elements within the company. The views and perceptions of participants within the process are critical for understanding the rationale associated with any process deviations. This approach has been used for understanding other aspects of engineering design, such as the research culture [ 44 , 45 ], change management in automation and manufacturing [ 34 , 46 ], and capstone design effectiveness [ 47 , 48 ]. Alternative approaches in case study research in engineering design are more generally focused on document analysis, focusing on the objectivity of analyzing existing information rather than seeking to extract potential explanations or perceptions. Document analysis in the case study has been used to understand information loss [ 49 ], design tool use [ 50 , 51 ], or problem-solution detailing [ 52 – 54 ].
For this case study, an automotive OEM was identified that presented a potential to study both the difference between engineering and manufacturing groups in the organization as well as studying the general cultural differences between the groups. The manufacturing facility is located in the Southeast US, while the engineering and management offices are located in Europe. The development headquarters and engineering teams are responsible for design and development of three brands. The manufacturing facility is responsible for the assembly of four vehicle models for one of these brands. The development headquarters employs nearly 20,000 employees across all major functions, while the production plan employs approximately 9000 employees across manufacturing and production activities. Both organizations employ a company-specific permanent engineering change management system, while the production plant also employs internal systems for temporary engineering change management.
Further, this case study was developed to be conducted while the first author was employed at the organization during a graduate internship that spanned roughly nine months. Further, the first author is fluent in both languages that are commonly used within the organization. This allowed the research team to not only literally translate interview and survey information collected, but to also add contextual understanding as appropriate. Finally, the research team had extensive contacts within this organization that spanned multiple decades. This was crucial in that trust had been established through multiple mechanisms that helped encourage multiple interviewees and survey respondents to participate without hesitation or reservation.
While specific details of the engineering change examples are not provided here for proprietary concerns, an illustrative example is presented. The seatbelt receiver in the passenger front seat might be found to rub on the center console, creating minor scratches that could be viewed negatively by the end-user. Therefore, a solution is needed to quickly respond to this quality defect. Locally, the manufacturer could decide to use a soft, felt pad on a sticker to attach to the seatbelt receiver. This could be immediately implemented to address the problem (temporary change), but it would still need to be submitted as an engineering change notification to the engineering group. This change would follow the defined engineering change management process as it is a product deviation. Any changes to the steps for assembly or the tools used are not considered changes to the product and are therefore not submitted as part of the change management process unless the assembly steps or fixtures are explicitly defined as required by the engineering department.
3.2 Phase I: Interviews.
The research procedure for this case study consisted of interviews and surveys. The interview process will be outlined in the ensuing subsections and is followed by the results. The interviews were used primarily to narrow down employee responses to a list of issues and topics that could be used for conducting a survey. A sample of interview questions can be seen in Table 2 .
Sample interview questions
Note: P: Process and W: Workload.
The questions in Table 2 were selected because they point toward the targeted nature of questions that were asked during the interview. It was important to find out whether or not the official P-EC process is actually used or if there are deviations. This allows for a starting point in investigating problems. Question 2 was included for a similar reason- if users think about how much time they spend with the problems created by the process and software system, they may be more inclined to actively participate in the interview. The last question is an example of a question that was added to later revisions of the interview list based on previous interviews during which it was mentioned that there is a problem with the P-EC notification system. The final set of interview questions consisted of 26 questions.
3.2.1 Finding Interview Participants.
To identify the P-EC process and obtain details about the software system in use, a focal point was to ask individuals with varying degrees of system interaction and responsibilities in the process. Furthermore, weaknesses in the process and systems were discovered through this approach. A tracking system used by the company was searched to identify interview candidates. This system tracks participants, roles, and timing for all engineering changes for specific models over a period of time that can be set by the user. Other companies track similar information [ 55 ].
The search was narrowed to a period of January 1, 2014, to December 31, 2015, and models that are produced at one particular manufacturing plant in the United States. The time was narrowed to this period because it gave a large enough sample size to be able to segment participants into user frequency groups (UFG), while minimizing the number of people who have moved on to other functions or other employment opportunities. Additionally, interview representation from all major departments at the OEM was sought. These departments are development, purchasing, production, and a group called “other,” describing those employees who do not fall into the other three departments.
The users, defined as those employees who have access to the system and are requested to give feedback, were then divided into user frequency groups, each user being a high-, medium-, or low-volume user. For example, a user who has given feedback 40 times over the course of a year would be in user frequency group “High.” An overview of this categorization can be seen in Table 3 .
Definition of UFG
3.2.2 Interview Execution.
The interviews were conducted in the native language of the interviewee. Each interview lasted between 30 and 60 min and was audio recorded after consent was obtained. The interviews were conducted in neutral locations, such as conference rooms or empty breakrooms. The interviewees were generally pleased that this study was being undertaken with comments such as “It’s about time someone looks at this system [translated]” and “throughput times that are pretty much completely pointless… with all the shadow lists that are being created off-line [translated]”. Further, the “low frequency” users were generally surprised to be included in the interview process.
3.2.3 Interview Results.
Results regarding the employees and the software system were gathered. All interviewees stated that their work requires face-to-face meeting time as well as phone conversations to complement the information that is in the P-ECM software system. None of the 15 who were interviewed had familiarity with other engineering change processes, as they had not worked at any other companies.
One difference among the interviewed associates is how much time it takes for them to work on a request, including data entry as well as meetings. This ranged between a few minutes and several hours, regardless of the department.
Additional differences came in the form of the final question, when associates were asked to give feedback on any other struggles they have with the process or the system. The process efficiency (“ The ineffable throughput times that are pretty much completely pointless… with all the shadow lists that are being created off-line, it’s really not efficient ” [translated]) and the quality of information (“ The quality of the information we receive isn’t always good ” [translated]), as well as the timing that is automatically generated for change requests, were the most frequently mentioned criticisms. Furthermore, the purchasing department had specific criticisms of the system and the workflow. Another interviewee was not pleased with getting requests that have no impact on him, saying, “ If somebody would just use their brain for once and think, ‘yeah that part number is affected but there is no change’ that would really help out ” [translated].
3.3 Phase II: Surveys.
To obtain additional data, a survey was used to receive more feedback. The following subsections detail the steps in creating the survey, finding survey participants, and distributing the survey.
3.3.1 Creating the Survey.
Based on the information gathered in the interviews, a survey consisting of 29 questions was created that was submitted to additional persons identified by the company tracking system. The survey was used to triangulate information obtained in the interviews. Prior to giving out the survey, it was tested on three individuals who had also completed interviews to ensure the questions reflected the current issues of the process and system and could be answered without needing clarification [ 56 ]. While the participants in the survey remained anonymous, the first section of the survey consisted of questions that made it possible to group the participant into different groups. For example, the participant was asked whether or not he still uses the engineering change system and how many years he has used the system.
The next section of the survey gave the participant the chance to indicate to which extent they agree with a statement that was made on the survey by marking it on the line. An example of this can be seen in Table 4 .
Excerpt from survey
Lastly, the users had three free response questions asking them if there are other issues with the system, other ways to improve the system, and how much time they could save with an improved system.
3.3.2 Finding Survey Participants.
The participants for the survey were found using the same approach as finding the participants for the interviews. It was based on the data management system that the OEM uses and was then filtered for those participants with the highest use of the engineering change management system. Fifty participants were sent the survey. The list was continually expanded, following the same selection protocol, until 46 individuals completed the survey.
3.3.3 Distributing the Survey.
Upon receiving the participant’s written consent, the survey was distributed in person, making it possible to personally thank the participant for his time. The survey distribution was completed for three weeks to account for the availability of all participants. The participants were asked to complete the survey in one week. The surveys were then collected as the participants finished them, also for three weeks.
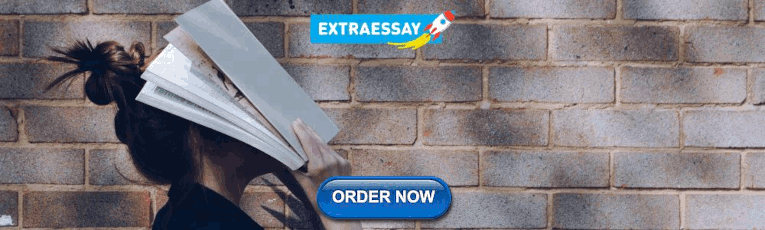
3.4 Survey Findings.
In total, 46 surveys were handed out and completed. The answers to two of the introductory questions (department and the number of uses per week) can be seen in Table 5 .
Demographic data
In addition to the data shown in Table 5 , the participants reported an average of 6 years of use in the software system that guides the P-EC process. Furthermore, participants required on average approximately one hour to complete their task regarding an engineering change request. This number includes meeting times, working in the system, and ensuring that all information is correct. However, the range of values given for this question is between 5 min and 7 h. Employees working in development took longer than their counterparts in other departments did.
To analyze the data, a measurement of the mark that was made on the survey for each question was taken. The further to the right the mark is, the more strongly a participant agreed with the statement (see Table 4 ). The data were recorded in a spreadsheet and were grouped by department, use, and experience level of the participant. Initially, every question was grouped by department, and the average was taken. Additionally, a total average for every question was taken. The total average is first used as a baseline for which topics the participants felt most strongly about based on either high or low values on the scale from 0 to 8.0. The raw data can be seen graphically in Fig. 1 .

Plots of average survey responses
A review of Fig. 1 reveals that all questions have a standard deviation between 1.7 and 2.2 with the exception of the last question, which has a standard deviation of 1.3. The next step in the analysis is to look at differences between the departments, company experience, and uses per week. This is the topic of the next section.
Analysis of differences is completed on several different groups: departments, number of uses per week, and number of years of experience. To examine whether or not statistical differences between responses exist, a Mann–Whitney U-test was used. This test is explained in further detail in the next subsection.
4.1 Mann–Whitney U-Test.
A Mann–Whitney U-test is used because of its ability to handle non-normal, discrete, or continuous data [ 57 ]. To use this type of test, the data must exhibit characteristics and/or be exposed to the assumptions displayed in Table 6 .
Assumptions for Mann–Whitney U-test
The nomenclature for these equations can be seen in Table 7 .
Nomenclature for Mann–Whitney U-test
Two sets of data are compared using Eqs. (1) and (2) . The comparison follows on the basis of the number of samples in each data set as well as the data rank. For each comparison that is conducted, a value for U 1 and a value for U 2 are generated. The lower of the two U values is then compared to a table of values for this test, which gives a critical value based on the number of samples in each data set and the significance level, α . For the comparisons in this thesis, α = 0.05 was used because it is frequently used in studies where a particular result is expected [ 59 ].
The null hypothesis is the following: H 0 = there is no significant difference between the data sets. This hypothesis is rejected if the calculated value for either U 1 or U 2 is lower than the critical value obtained from the table (i.e., U 1 < U α =0.05 or U 2 < U α =0.05 ) [ 57 ]. The test was run using IBM SPSS Statistics 23.
4.2 Differences Between Departments.
Using the Mann–Whitney U-test, all of the statements presented can be analyzed for the significance of the differences in the data. The focus of the data analysis is on differences between the development department and the production department for the following reason: the development department most frequently generates an engineering change and therefore may exhibit bias toward any issues with the perceived quality of engineering changes, whereas the production department is generally the end-user/customer of the engineering change, and must implement changes. Conducting the test on these two departments reveals the following information, summarized in Table 8 . It is important to note that the significant results are influenced by the number of participants in each group. Since not all participants answered all questions, a different sample size occurred for some questions. The change in sample size leads to a change in the U critical .
Summary of significance in statement means for departments
Note: s: significant, ns: not significant.
Statements 15, 18, 23, and 24 indicate significant differences between the development and the production department. To understand what can explain these differences, the statements are reproduced in Table 9 .
Restatement of statistically significant survey statements (department)
Statement 15 shows a difference because the production department may rely very heavily on the information that is in the engineering change and may be particularly weary of giving feedback since the members of the production department must ultimately implement changes.
The difference in statement 18 may stem from the fact that a creator of an engineering change needs the feedback of multiple production department employees while not needing as many feedbacks from his own department because he is solely responsible for a part.
The difference in answers to statement 23 may be explained by the fact that the development department, as the creator of the engineering change, does not want to fill out more information, while it would help the production department receive more information to provide informed feedback.
Statement 24 may also be attributed to these differences, though it should be noted that all departments felt strongly about this statement.
4.3 Differences Between the Number of Uses/Week.
The distinction of how many times the software is used per week is another comparison that can be made. For this comparison, those who give feedback on 10 or more changes per week are compared to those who give zero to two feedbacks per week. The results of this comparison can be seen in Table 10 .
Summary of significance in statement means for use
Table 10 summarizes that none of the differences between those participants who use the system zero to two times and more than 10 times are significant. While it may seem initially that the averages of those two groups, as seen in Table 10 , are very far apart on some questions, the small sample size of this comparison resulted in comparison to very low U crit values, which resulted in accepting the null hypothesis for every question and therefore accepting that there is no significant difference between the two data samples.
4.4 Differences Between the Years of Use.
Finally, the differences in terms of experience levels were analyzed. In this case, those participants who had used the system for at least 10 years were compared with those who were novices, having less than 2.5 years of experience. The results from this comparison can be seen in Table 11 .
Summary of significance in statement means for experience
A review of Table 11 shows that Statements 8, 9, 13, and 18 indicate significant differences in responses based on experience level. To understand what can explain these differences, the questions are reproduced in Table 12 .
Restatement of statistically significant survey statements (experience)
The statements in Table 12 indicate that, when employees start using the engineering change software system, they feel that the transparency of the process and the usability of the software needs to be improved. It is therefore likely that the employee perception of usability and transparency increases the more they use it. Additionally, there is an expectedly large difference for statement 13 because new users, who are unfamiliar with the process and software, will most likely not help others in a similar position. The response to Statement 18 can be explained in a similar fashion. If the user is a novice user, it is more likely that others in the department will receive a feedback request on the same topic, to ensure that a more knowledgeable employee also knows of a potential change.
4.5 Shared Differences.
The data presented here indicate very few shared differences between the different groups that were compared. The only statement that created statistically significant differences for various groups was Statement 18, which appeared in the department comparison and the years of experience comparison.
Do the employees have any issues with the engineering change management process or tool?
Based on the information provided in Sec. 3 of this paper, the employees do have issues with the engineering change management process or tool. Examples include lacking quality in the engineering change feedback requests and lack of notifications when information is altered in the request. However, it must also be noted that overall, the question “does this software make your work harder?” was generally answered on the “disagree” end of the spectrum.
If so, can these issues be broken down into differences between departments?
These issues and many other statements can be broken down into statistically significant differences between departments and years of experience. Grouping by the number of uses per week did not reveal any statistically significant differences. A shared difference between departments and years of experience exists regarding other employees receiving feedback requests on the same topic. This may be an opportunity to cut costs for the OEM.
5.1 Generalizability.
While this is a case study that explores a single organization and its implemented engineering change management process for supporting line-sustaining engineering, the findings can be generalized and applied beyond this specific organization. First, automotive OEMs might have different approaches to product development, but they are constantly sharing best practices through exchange programs and research literature. These organizations are generally multinational with engineering in one country and products distributed internationally. Thus, the design-manufacturing division is often reinforced by multiple national cultures. The findings within this case study can have potential generalization to other automotive organizations of similar structure and configuration.
In addition to direct transferability to other automotive or other complex systems design and manufacturing organizations, there is the potential to generalize the findings that the process that is implemented to support a specific activity and a defined key performance indicator can be modified and corrupted without malicious intent through the introduction of shadow systems. This is something that should be incorporated into company process development as a consideration. While it is commonly suggested that key performance indicators are often used incorrectly, this case study presents evidence of this. At the same time, it presents an approach to help uncover these deficiencies through systematic analysis through interactions with employees.
Ultimately, the goal of this research is not to present a universal truth, but to add to the understanding of how engineering change management operates in industrial practice. This can help inform the future development of processes and supporting tools.
5.2 Study Limitations.
A limitation of this case study is that the data in the form of interviews and survey results were only analyzed on one product line at one automotive OEM. The perceived issues are only valid for the associates of the product line that were interviewed and could be different when interviewing associates who work on the engineering change request for a different product line within the same company.
5.3 Future Work.
Building off this research and its limitations, many other avenues can be pursued. Similar analysis involving more product lines at this OEM and/or other OEMs throughout the world. The differences between companies could give insights into best practices regarding software use and process flow. These best practices could then lead to cost savings across the industry. Furthermore, an increase in the number of survey participants would help strengthen the case made in this paper as well. Another opportunity to further research engineering change management deals with a detailed analysis of the impact of past engineering changes. Many engineering changes are presented as cost savings; investigating whether or not these cost savings were realized or not can be beneficial to an organization in handling engineering changes. This leads to the following research question: “What percentage of all part engineering changes have a positive long-term value?”
This work can be used as a framework for other industry case studies on manufacturing change management. For instance, this structured interview and survey approach has already been used in a study on “de-automating” aircraft assembly workstations [ 46 ]. Having a defined structure for how to conduct this research is critically important for supporting future studies.
There are no conflicts of interest. All procedures performed for studies involving human participants were in accordance with the ethical standards stated in the 1964 Declaration of Helsinki and its later amendments or comparable ethical standards. Informed consent was obtained from all participants. Documentation is provided upon request. Informed consent is not applicable. This article does not include any research in which animal participants were involved.
The data sets generated and supporting the findings of this article are obtainable from the corresponding author upon reasonable request.
Get Email Alerts
Related articles, related proceedings papers, related chapters, affiliations.
- Accepted Manuscripts
- About the Journal
- Editorial Board
- Information for Authors
- Call for Papers
- Rights and Permission
- Online ISSN 2770-3495
ASME Journals
- About ASME Journals
- Submit a Paper
- Title History
ASME Conference Proceedings
- About ASME Conference Publications and Proceedings
- Conference Proceedings Author Guidelines
ASME eBooks
- About ASME eBooks
- ASME Press Advisory & Oversight Committee
- Book Proposal Guidelines
- Frequently Asked Questions
- Publication Permissions & Reprints
- ASME Membership
Opportunities
- Faculty Positions
- ASME Community
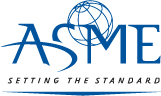
- Accessibility
- Privacy Statement
- Terms of Use
- Get Adobe Acrobat Reader
This Feature Is Available To Subscribers Only
Sign In or Create an Account
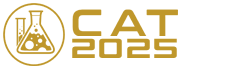
Victor Mukhin
- Scientific Program
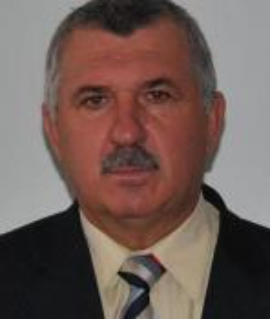
Title : Active carbons as nanoporous materials for solving of environmental problems
However, up to now, the main carriers of catalytic additives have been mineral sorbents: silica gels, alumogels. This is obviously due to the fact that they consist of pure homogeneous components SiO2 and Al2O3, respectively. It is generally known that impurities, especially the ash elements, are catalytic poisons that reduce the effectiveness of the catalyst. Therefore, carbon sorbents with 5-15% by weight of ash elements in their composition are not used in the above mentioned technologies. However, in such an important field as a gas-mask technique, carbon sorbents (active carbons) are carriers of catalytic additives, providing effective protection of a person against any types of potent poisonous substances (PPS). In ESPE “JSC "Neorganika" there has been developed the technology of unique ashless spherical carbon carrier-catalysts by the method of liquid forming of furfural copolymers with subsequent gas-vapor activation, brand PAC. Active carbons PAC have 100% qualitative characteristics of the three main properties of carbon sorbents: strength - 100%, the proportion of sorbing pores in the pore space – 100%, purity - 100% (ash content is close to zero). A particularly outstanding feature of active PAC carbons is their uniquely high mechanical compressive strength of 740 ± 40 MPa, which is 3-7 times larger than that of such materials as granite, quartzite, electric coal, and is comparable to the value for cast iron - 400-1000 MPa. This allows the PAC to operate under severe conditions in moving and fluidized beds. Obviously, it is time to actively develop catalysts based on PAC sorbents for oil refining, petrochemicals, gas processing and various technologies of organic synthesis.
Victor M. Mukhin was born in 1946 in the town of Orsk, Russia. In 1970 he graduated the Technological Institute in Leningrad. Victor M. Mukhin was directed to work to the scientific-industrial organization "Neorganika" (Elektrostal, Moscow region) where he is working during 47 years, at present as the head of the laboratory of carbon sorbents. Victor M. Mukhin defended a Ph. D. thesis and a doctoral thesis at the Mendeleev University of Chemical Technology of Russia (in 1979 and 1997 accordingly). Professor of Mendeleev University of Chemical Technology of Russia. Scientific interests: production, investigation and application of active carbons, technological and ecological carbon-adsorptive processes, environmental protection, production of ecologically clean food.
Quick Links
- Conference Brochure
- Tentative Program

Thermodynamics of titanium oxides in metallurgical slags
- Published: 02 September 2015
- Volume 2015 , pages 346–353, ( 2015 )
Cite this article
- A. V. Alpatov 1 &
- S. N. Paderin 2
72 Accesses
Explore all metrics
The energy parameters of the model of a pseudoregular ionic solution are estimated for binary oxide phase diagrams in seven systems containing titanium oxide. The obtained parameters are compared to the available theoretical and experimental data on the thermodynamic properties of TiO 2 in liquid binary systems. The model of a pseudoregular ionic solution is extended to the liquid eight-component FeO-MnO-CaO-MgO-SiO 2 -CrO 1.5 -AlO 1.5 -TiO 2 system, as applied to metallurgical slags containing titanium oxides.
This is a preview of subscription content, log in via an institution to check access.
Access this article
Price includes VAT (Russian Federation)
Instant access to the full article PDF.
Rent this article via DeepDyve
Institutional subscriptions
Similar content being viewed by others
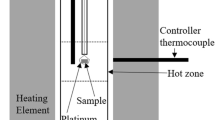
Phase Equilibrium Study of the CaO-SiO2-MgO-Al2O3-TiO2 System at 1300°C and 1400°C in Air
Junjie Shi, Min Chen, … Ari Jokilaakso
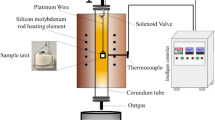
Phase Equilibria of Ti-bearing Electric Furnace Slags in the CaO-MgO-SiO2-13%Al2O3-50%TiO2 System
Jianfa Jing, Shuai Wang, … Lingzhi Yang
Thermodynamic Analysis of the Deoxidizing Ability of Strontium in Liquid Iron in the Presence of Aluminum
L. A. Makrovets, O. V. Samoilova, … I. V. Bakin
N. A. Smirnova, Molecular Theory of Solutions (Khimiya, Leningrad, 1987).
Google Scholar
A. V. Senin, O. V. Kuznetsova, A. A. Lykasov, et al., “Calculation of the activities of the components of oxide melts in terms of the model of an ideal solution of interaction proiducts,” in Structure and Properties of Metallic and Slag Melts. Vol. 3. Structure and Properties of Slag Melts (YuUrGU, Chelyabinsk, 2004).
V. A. Kozheurov, Thermodynamics of Metallurgical Slags (Metallurgiya, Sverdlovsk, 1955).
Ban-Ya Shiro and Jae-Dong Shim, “Application of regular solution model for the equilibrium of distribution of oxygen between liquid iron and steelmaking slags,” Can. Met. Quart. 21 (4), 319–328 (1982).
Article Google Scholar
Shiro Ban-Ya, “Mathematical expression of slag–metal reaction in steelmaking process by quadratic formalism based on the regular solution model,” ISIJ Intern. 33 (1), 2–11 (1993).
E. M. Vil’gel’m and G. G. Mikhailov, “On the application of the thermodynamics of ionic melts,” in Physicochemical Studies of Metallurgical Processes (UPI, Sverdlovsk, 1978), Vol. 6.
A. D. Pelton and M. Blander, “Thermodynamic analysis of ordered liquid solutions by modified quasichemical approach—application to silicate slags,” Met. Trans. B 17 , 805–815 (1986).
V. I. Antonenko and D. Ya. Povolotskii, “Electrostatic version of the theory of ionic solutions and its application to calculating the metal–slag interaction,” Izv. Chelyab. Nauchn. Tsentra UrO RAN, No. 2 , 71–80 (1999).
D. R. Gaskell, “Thermodynamic models of liquid silicates,” Can. Met. Quart. 20 (1), 3–19 (1981).
P. Sastri and A.K. Lahiri, “Applicability of central atom models to binary silicate and aluminate melts,” Met. Trans. B 16 , 325–331 (1985).
A. G. Ponomarenko, “Problems of the thermodynamics of phases of variable compositions that have a collective electron system: I. The free energy of the phase,” Zh. Fiz. Khim. XLVIII (7), 1668–1671 (1974).
A. G. Ponomarenko and E. P. Mavrenova, “Problems of the thermodynamics of phases of variable compositions that have a collective electron system: I I. Estimation of the energy parameters,” Zh. Fiz. Khim. XLVIII (7), 1672–1674 (1974).
S. N. Paderin and A. V. Alpatov, “Energy parameters in the model of regular ionic solutions as applied to metallurgical slags,” Elektrometallurgiya, No. 9 , 34–41 (2008).
Atlas of Slags , (Metallurgiya, Moscow, 1985).
E. T. Turkdogan, Physical Chemistry of High Temperature Technology (Academic, New York, 1980).
G. Eriksson and A.D. Pelton, “Critical evaluation and optimization of the thermodynamic properties and phase diagrams of the MnO–TiO 2 , MgO–TiO 2 , FeO–TiO 2 , Ti 2 O 3 –TiO 2 , Na 2 O–TiO 2 and K 2 O–TiO 2 systems,” Met. Trans. B 24 , 795–805 (1993).
Y. Q. Hou, G. Xie, D. P. Tao, and X. H. Yu, “Application of modified quasi-regular solution model to binary metallurgical molten slag systems,” J. Iron Steel Res. Intern. 17 (10), 13–17 (2010).
Shiro Ban-Ya, A. Chiba, and A. Hikosaka, “Thermodynamics of Fe t O–M x O y (M x O y = CaO, SiO 2 , TiO 2 and Al 2 O 3 ) binary melts in equilibrium with solid iron,” Tetsu-to-hagane 66 , 1484–1493 (1980).
Y. B. Kang and H. G. Lee, “Experimental study of phase equilibria in the MnO–“TiO 2 ”–“Ti 2 O 3 ” system,” ISIJ Intern. 45 (11), 1543–1551 (2005).
B. K. D. P. Rao and D. R. Gaskel, “The thermodynamic activity of MnO in melts containing SiO 2 , B 2 O 3 and TiO 2 ,” Met. Trans. B 12 , 469–477 (1981).
T. G. Kim, W. K. Lee, J. H. Park, D. J. Min, and H. S. Song, “Sulfide capacity and phase equilibria of MnO–TiO 2 –MnS system at1723K,” ISIJ Intern. 41 (12), 1460–1464 (2001).
M. Ito, K. Morita, and N. Sano, “Thermodynamics of the MnO–SiO 2 –TiO 2 system at1673K,” ISIJ Intern. 37 (9), 839–843 (1997).
M. Ohta and K. Morita, “Thermodynamics of the MnO–Al 2 O 3 –TiO 2 system,” ISIJ Intern. 39 (12), 1231–1238 (1999).
A. S. Berezhnoi, Multicomponent Oxide Systems (Naukova Dumka, Kiev, 1970).
Download references
Author information
Authors and affiliations.
Baikov Institute of Metallurgy and Materials Science, Russian Academy of Sciences, Leninskii pr. 49, Moscow, 119991, Russia
A. V. Alpatov
OAO Elektrostal’ Metallurgical Works, Elektrostal’, Moscow oblast, Russia
S. N. Paderin
You can also search for this author in PubMed Google Scholar
Corresponding author
Correspondence to A. V. Alpatov .
Additional information
Original Russian Text © A.V. Alpatov, S.N. Paderin, 2015, published in Metally, 2015, No. 3, pp. 11–18.
Rights and permissions
Reprints and permissions
About this article
Alpatov, A.V., Paderin, S.N. Thermodynamics of titanium oxides in metallurgical slags. Russ. Metall. 2015 , 346–353 (2015). https://doi.org/10.1134/S003602951505002X
Download citation
Received : 21 July 2014
Published : 02 September 2015
Issue Date : May 2015
DOI : https://doi.org/10.1134/S003602951505002X
Share this article
Anyone you share the following link with will be able to read this content:
Sorry, a shareable link is not currently available for this article.
Provided by the Springer Nature SharedIt content-sharing initiative
- Phase Diagram
- RUSSIAN Metallurgy
- Energy Parameter
- Find a journal
- Publish with us
- Track your research
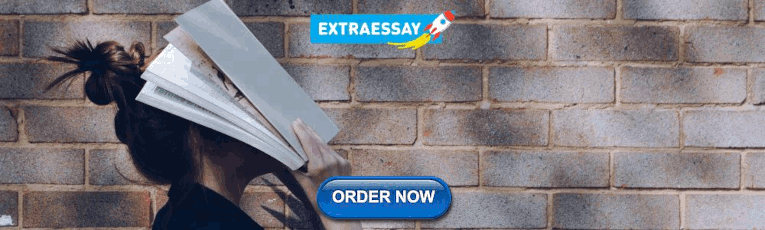
IMAGES
VIDEO
COMMENTS
Features: Discusses automotive manufacturing processes in a comprehensive manner with the help of applications. Provides case studies addressing issues in the automotive industry and manufacturing operations in the production of vehicles. Discussion on material properties while laying emphasis on the materials and processing parameters.
Features: Discusses automotive manufacturing processes in a comprehensive manner with the help of applications. Provides case studies addressing issues in the automotive industry and manufacturing operations in the production of vehicles. Discussion on material properties while laying emphasis on the materials and processing parameters.
Download Citation | On May 18, 2023, G.K. Awari and others published Automotive Manufacturing Processes: A Case Study Approach | Find, read and cite all the research you need on ResearchGate
Discusses automotive manufacturing processes in a comprehensive manner with the help of applications. Provides case studies addressing issues in the automotive industry and manufacturing operations in the production of vehicles. Discussion on material properties while laying emphasis on the materials and processing parameters.
In this study, we emphasize the latest development and traceability studies for automotive manufacturing and compare their performance. This study will provide an indication to the manufacturers to select the most suitable traceability methodology for their product. The main stages involved in the auto manufacturing process are depicted in ...
Automotive Manufacturing Processes: A Case Study Approach eBook : Awari, G.K., Kumbhar, V.S., Tirpude, R.B., Rajurkar, S.W.: Amazon.ca: Kindle Store
1. Quantitative Techniques in Business, Management and Finance: A Case study approach. 2. Automotive Systems: Principles and Practice. 3. Additive Manufacturing and 3D Printing Technology: Principles and Practice. 4. Ethics in Information Technology Dr. Awari is recognised Research Supervisor at 4 Indian universities. Total 18 (eighteen ...
Lean Manufacturing Practices Assessment. Case Study of Automotive Company. Patrycja Hąbek1* , Juan J. Lavios2, A da m Grzywa 3. 1 Faculty of Organization and Management, Silesian University of ...
Case Study: How Technology is Helping Automotive Manufacturers Achieve Sustainable Goals. Car manufacturers face a range of challenges globally as they strive to move towards sustainable manufacturing. Central to this is ensuring production processes remain as clean and efficient as possible while maintaining product quality and reducing wastage.
Discusses automotive manufacturing processes in a comprehensive manner with the help of applications. Provides case studies addressing issues in the automotive industry and manufacturing operations in the production of vehicles. Discussion on material properties while laying emphasis on the materials and processing parameters.
Abstract and Figures. Smartness and agility are two quality measures that are pragmatic to achieve a flexible, maintainable, and adaptable system in any business. The automotive industry also ...
2 Manufacturing Process Description In order to investigate the integration between PLM and MES, a case-study in the field of automotive manufacturing is presented. The process at stake consists in a laser welding operation: it is a process that obtains fusion by directing a highly concentrated beam of coherent light on a very small spot.
The objective of the study is to use a real-time case-based approach to determine how lean methodologies like VSM, LB, and Kanban can be utilized to improve the current and existing processes and establish a better inventory and process control. The data collection is done in an automotive component manufacturing industry based in Pithampur, India.
Few papers have dealt with the process of servitization at the firm level. There has been a particular lack of research in manufacturing. Business model innovation through convergence between products and services is an indispensable aspect of a firm's sustainable strategy. The current paper analyzes servitization as a process innovation by performing a single case study of a manufacturing firm.
In this study, we emphasize the latest development and traceability studies for automotive manufacturing and compare their performance. This study will provide an indication to the manufacturers to select the most suitable traceability methodology for their product. The main stages involved in the auto manufacturing process are depicted in Figure1.
Abstract. Due to interest in aspects such as process, strategies, and tools of engineering changes expressed in a literature review, a case study was done on a major automotive original equipment manufacturer (OEM) to assess the perceived quality of its part engineering change management process and supporting system through its employees' eyes. A combination of 12 interviews lasting 12 h ...
Results of advancement of the process of production of rolled stock from steel R6M5 are considered. The effect of various process factors on the quality parameters of the steel is discussed. An analysis of actual data and of industrial experiments is presented.
Approach: A Case Study in the Automotive Indu stry . DOI: 10.12776/QIP.V25I2.1576 . Hanane Rifqi, Abdellah Zamma, Souad B. Souda, Mohamed Hansali ... manufacturing process. International Journal ...
Title : Active carbons as nanoporous materials for solving of environmental problems Abstract: However, up to now, the main carriers of catalytic additives have been mineral sorbents: silica gels, alumogels. This is obviously due to the fact that they consist of pure homogeneous components SiO2 and Al2O3, respectively.
Features: Discusses automotive manufacturing processes in a comprehensive manner with the help of applications. Provides case studies addressing issues in the automotive industry and manufacturing operations in the production of vehicles. Discussion on material properties while laying emphasis on the materials and processing parameters.
The obtained parameters are compared to the available theoretical and experimental data on the thermodynamic properties of TiO 2 in liquid binary systems. The model of a pseudoregular ionic solution is extended to the liquid eight-component FeO-MnO-CaO-MgO-SiO 2 -CrO 1.5 -AlO 1.5 -TiO 2 system, as applied to metallurgical slags containing ...
A very limited number of literature sources report on the study of the possibility of using microwave radiation for sintering UO2 fuel pellets. The authors have shown the promise of this sintering method by increasing the heating rate and reducing the holding time, thereby significantly reducing the sintering cycle of ceramic pellets. However ...