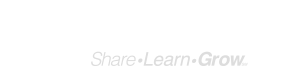
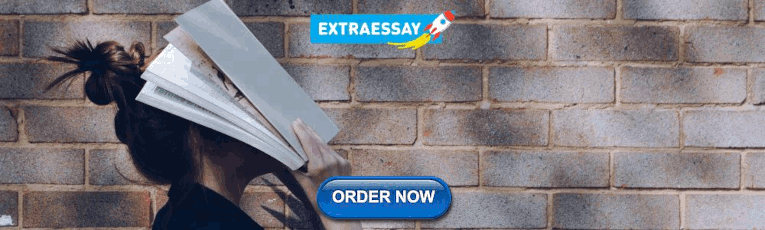
Search form
Sign Up or Sign In

Kata Resources
Toyota Kata was developed by Mike Rother, a researcher, engineer, teacher, author and speaker on the subjects of management, leadership, improvement, adaptiveness and change in human organizations. In his 2009 book, “Toyota Kata: Managing People for Improvement, Adaptiveness and Superior Results,” Rother describes Toyota Kata as a means for developing, activating and mobilizing human potential in a way that makes scientific thinking a daily habit.
In “The Toyota Kata Practice Guide,” Rother describes scientific thinking as, “a continuous comparison between what we predict will happen next, seeing what actually happens and adjusting our understanding and actions based on what we learn from the difference.”

Users can implement scientific thinking by practicing the Improvement Kata, which is one of the main elements within Toyota Kata. This Improvement Kata is a series of steps that provide a mindset for problem solving. These steps include:
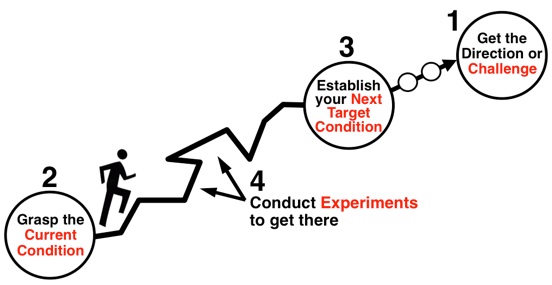
- Grasp the current condition. This step invites users to ask, “Where are we now?” and includes the gathering of data and information that sets up the next step.
- Establish the next target condition. Where do we want to go? What do we want to achieve? In this step, participants set tangible and measurable goals which include an achieve-by date, desired outcome and a general description of the process on how the target condition will be reached. Important to note, this step is part of the planning phase and is likely to change depending on the results of experimentation and achievement of milestones along the journey.
- Experiment toward the target condition. This step is part of the execution stage and includes the actions needed to reach the target condition. The path towards the target condition is typically not a straight line and usually involves obstacles. This step usually involves a process of rapid learning and discovery of the steps that are working and those which are not. In this step, adjustments are made on the way to the target condition.
The steps outlined in the Improvement Kata are designed to help users, no matter which problem-solving or improvement method they are using.
Implementing the Improvement Kata can be difficult because it often requires a new or different way of thinking and learners may revert to old patterns and habits. In addition, it can be difficult for learners to see where they are going wrong or making mistakes throughout the process. That’s where the other main element of Toyota Kata comes in. Known as the Coaching Kata, this element of Kata focuses on the practice of teaching the Improvement Kata pattern.
An Improvement Kata coach helps provides guidance and support for learners and can help speed up the learning process. The coach helps the learner overcome setbacks, provides encouragement and has a vested interest in helping the learner succeed. Coaching however, also takes practice.
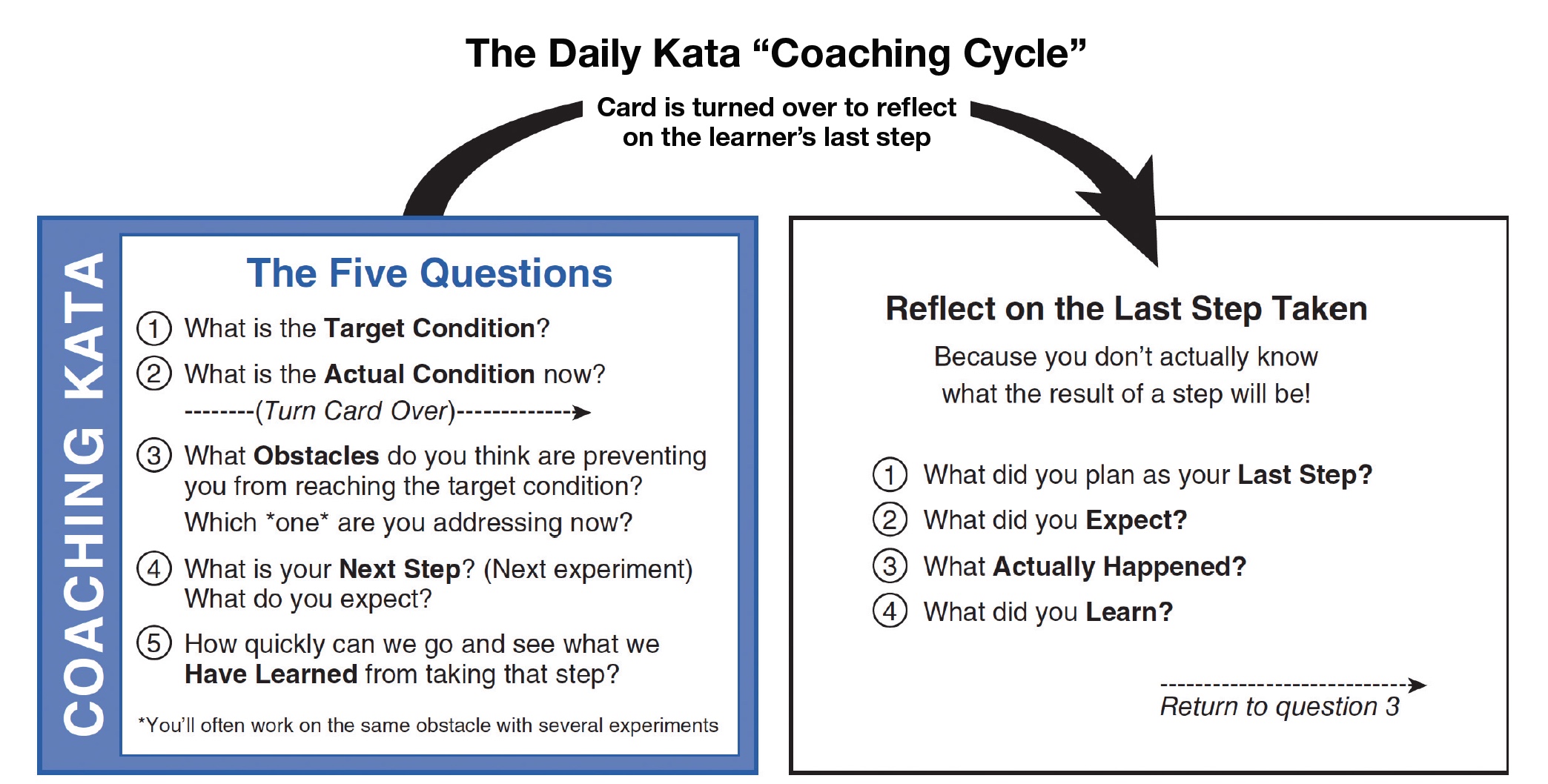
- What is the target condition? - What is the actual condition now? - What obstacles do you think are preventing your from reaching the target condition? Which one are you addressing now? - What is your next step? (Next experiment) What do you expect? - How quickly can we go and see what we have learned from taking that step?
These questions, considered the coaching cycle, help reinforce the pattern of the Improvement Kata and helps reveal how the learner is thinking. Typically, this pattern of coaching includes asking a question, listening, comparing (the learner’s response to the desired pattern of thinking), and instructing.
The use of these Coaching Kata questions takes practice. With feedback from a second coach, these skills can be improved and become more effective. For more detail on how to develop the scientific thinking skills of the Improvement Kata or the coaching skills of the Coaching Kata, consult Mike Rother’s “The Toyota Kata Practice Guide.” For more information about Toyota Kata visit Mike Rother's Toyota Kata website .
Images provided by Mike Rother
Mike Rother keynote at AME San Diego 2018:
Mike Rother's Kata in the Classroom session from AME San Diego 2018:
Mike Rother's Introduction to Kata video:
Compact Kata Online Course - $70 for AME Members
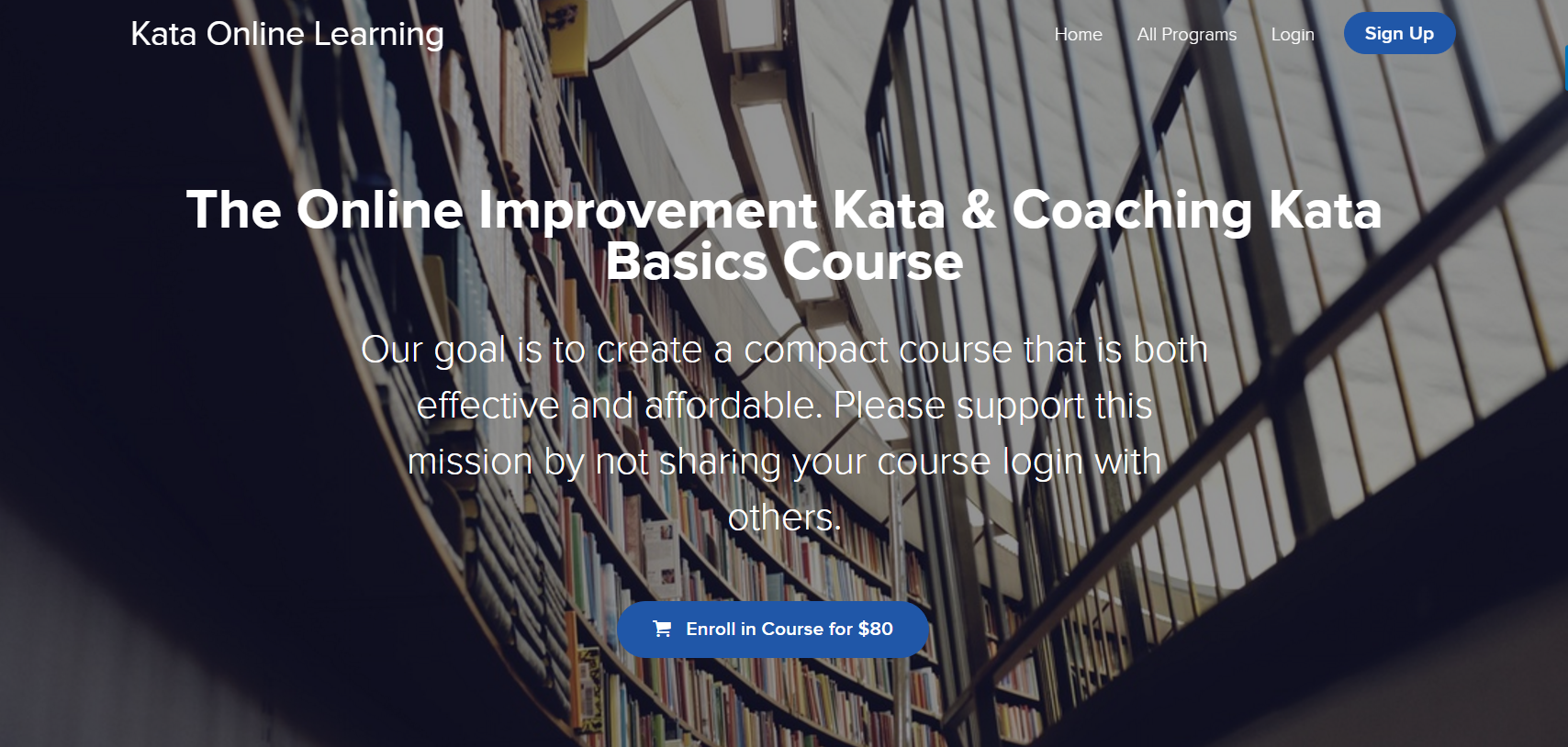
Take the Kata Course
Kata articles in target magazine:.
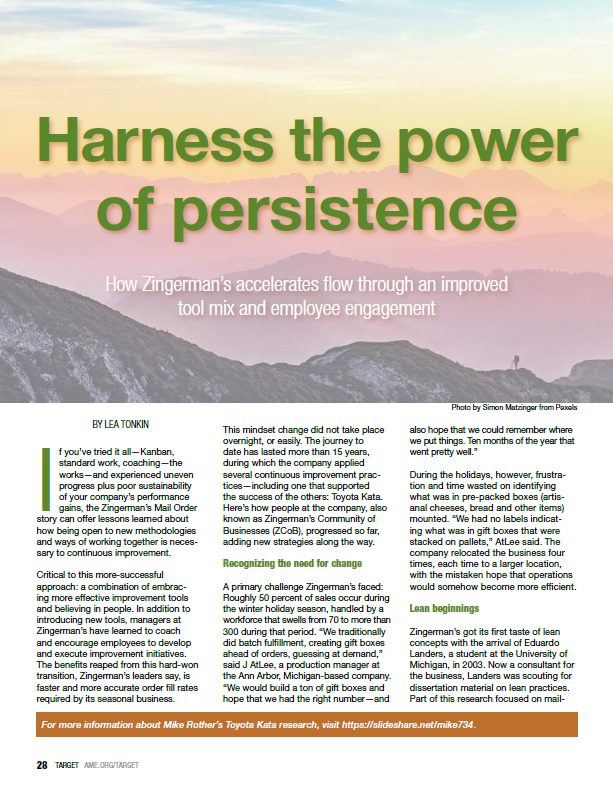
Additional Kata Articles/Resources:
- My Kata anniversary (Healthcare Quality Improvement blog 7/21/19) by Joy Furnival
- Toyota Kata Introduction to Kata video PowerPoint slides
- A family's growth fueled by crisis : The power of the Improvement Kata (Target Online 8/24/15) by Tyson Ortiz
- Why Toyota Kata May Be the Right Approach for You (Dan Markovitz (2/26/19)
- Agile LEGO - Toyota Kata an alternative to Retrospectives by Hakan Forss (4/25/19)
- Toyota Kata A3 Problem Solving by Mark Rosenthal (Quality Digest 2/24/14)
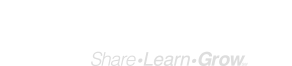
Mastering Problem-Solving and Decision-Making Skills with Toyota Kata
Toyota Kata is a methodology developed by Toyota to help organizations achieve continuous improvement. At its core, Toyota Kata is a set of practices that help individuals and teams to develop and improve their problem-solving and decision-making skills.
The word “kata” refers to movements or techniques practiced repeatedly until they become ingrained in the performer’s muscle memory. In the context of Toyota Kata, the term refers to practices designed to help individuals and teams develop the skills they need to improve continuously.
So, how does Toyota Kata work? At its core, Toyota Kata is based on experimentation and learning. The methodology involves a four-step process:
- Understand the direction: The first step in the Toyota Kata process is understanding the direction or goal. This involves clearly understanding what you are trying to achieve and why it is important.
- Grasp the current condition: The second step is to grasp the current condition. This involves clearly understanding the current situation and identifying any obstacles or challenges that must be overcome.
- Establish the target condition: The third step is establishing the target condition. This involves developing a clear vision of where you want to be and what you must do to get there.
- Conduct experiments: The fourth step is to conduct experiments. This involves testing different approaches and solutions to see what works and what doesn’t.
The Toyota Kata methodology is designed to be used on an ongoing basis. By following this process, individuals and teams can continuously experiment and learn, improving their problem-solving and decision-making skills.
So, what are the benefits of using Toyota Kata? One of the key benefits is that it helps to establish a culture of continuous improvement. By encouraging experimentation and learning, Toyota Kata helps create an environment where individuals and teams constantly look for ways to improve.
What do I get out of practicing KATA?
We gain a new meta-skill with frequent training to apply in all possible situations. Here are some examples:
- Improved adaptability to increasingly complex and dynamic situations.
- True daily continuous improvement becomes part of our business.
- Increased likelihood that we discover innovations through improved problem-solving skills.
- A way of leading includes an organic way of building a learning organization.
- The ability to learn new skills faster. 6) Find unique solutions to unique challenges.
Another benefit of Toyota Kata is that it helps to develop the problem-solving and decision-making skills of individuals and teams. By practicing the Toyota Kata techniques, individuals and teams can improve their ability to identify problems, develop solutions, and make decisions.
In conclusion, Toyota Kata is a powerful tool for any organization seeking continuous improvement. By following the four-step process of understanding the direction, grasping the current condition, establishing the target condition, and conducting experiments, individuals and teams can develop the problem-solving and decision-making skills they need to succeed. With its emphasis on experimentation and learning, Toyota Kata helps to create a culture of continuous improvement and sets organizations on a path to long-term success.
- More By sensei
- More In Blog
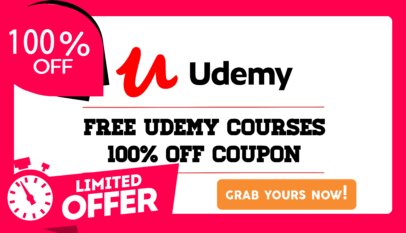
Free Udemy Courses 100% Coupon
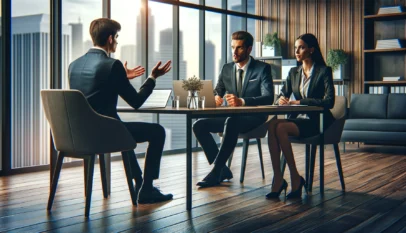
How to Ace Your Next Job Interview: Expert Insights and Strategies
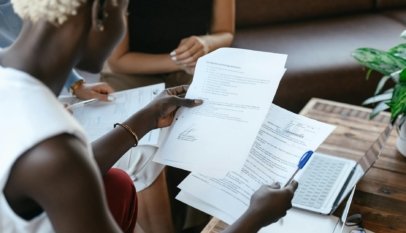
Mastering the Trio: Project, Program & Portfolio Management
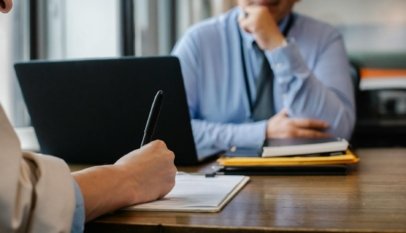
The Evolution of Performance Reviews: From Annual Appraisals to Continuous Feedback

Behaviors that kill employee motivation
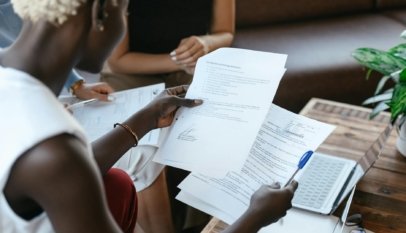
Common Interview Questions for Project Management Roles
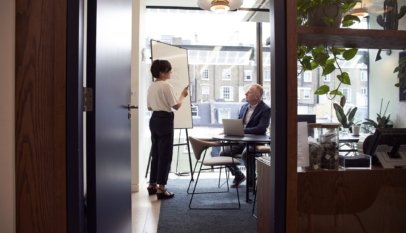
The Pillars of Corporate Success: Key Responsibilities of Top Executives
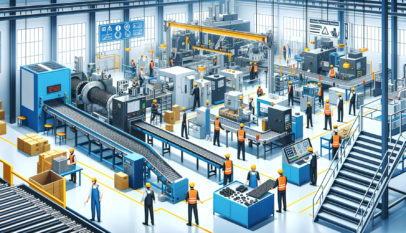
Navigating the 4M Changes in the Workplace: A Comprehensive Guide
Leave a reply cancel reply.
Your email address will not be published. Required fields are marked *
Notify me of follow-up comments by email.
Notify me of new posts by email.
Most Popular
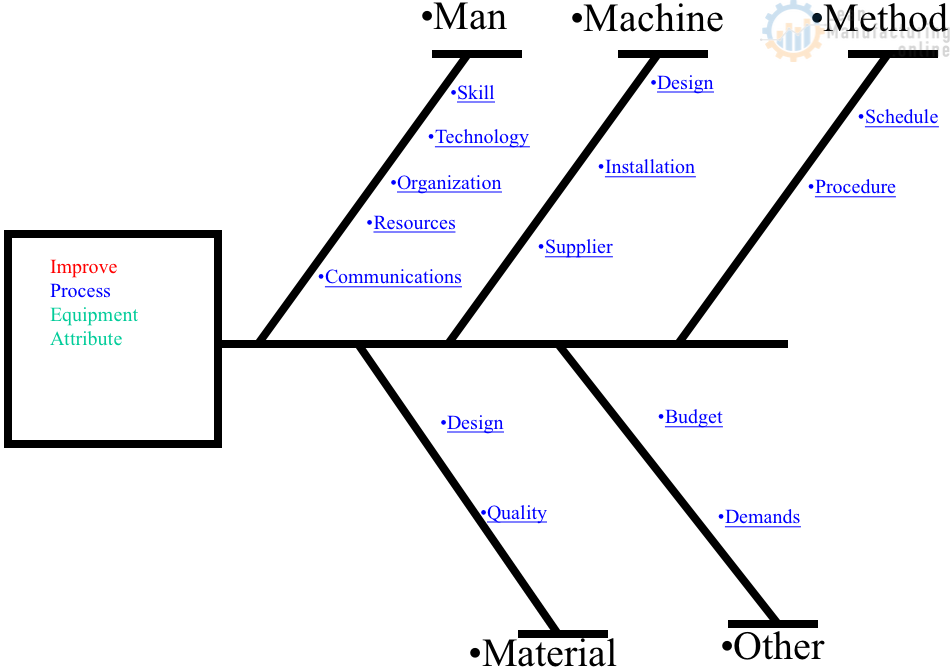
4M Analysis Process
The purpose of this procedure is to define the steps to do a 4M …

OPL – One Point Lesson Template – Free Download
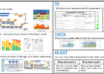
PDCA – A Process Approach
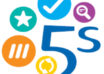
5S Audit Checklist and Report

Why-Why Analysis
Blog Search
Subscribe to blog via email.
Enter your email address to subscribe to this blog and receive notifications of new posts by email.
Email Address
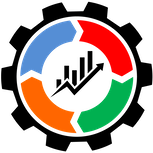
- Terms of Use
- Privacy Policy
- About Our Ads

An official website of the United States government
Here’s how you know
Official websites use .gov A .gov website belongs to an official government organization in the United States.
Secure .gov websites use HTTPS A lock ( Lock A locked padlock ) or https:// means you’ve safely connected to the .gov website. Share sensitive information only on official, secure websites.
https://www.nist.gov/blogs/manufacturing-innovation-blog/toyota-kata-lean-strategy-keeping-pace-change
Manufacturing Innovation Blog
Powered by the Manufacturing Extension Partnership
Toyota Kata: A Lean Strategy for Keeping Up with the Pace of Change
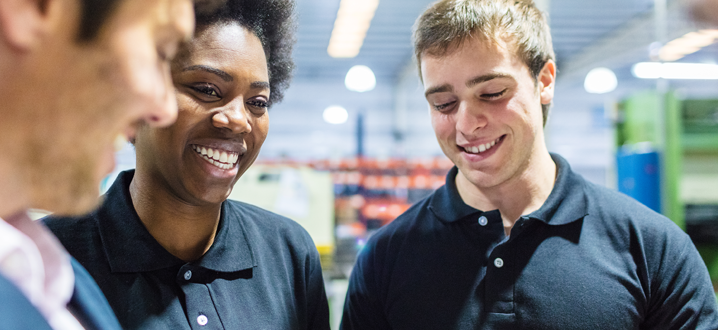
“Why are our changeovers taking so long?”
If you’ve asked this question on the shop floor, more than likely you were met with blank stares by your employees. Open-ended questions like this are overwhelming, so employees try to find quick answers that don’t really address the problem. They don’t have a starting point to form an answer.
But what if you asked a question with a specific, achievable goal?
“What steps can we take to reduce changeover time by 15 minutes?”
You’ve then provided your employees with a measurable goal in the form of a question. Your workers may feel empowered to answer with some hands-on suggestions for incremental changes, such as reducing setup steps or combining workstations. This in turn could not only reduce changeover time, but significantly eliminate wait times and inventories.
This approach is often described as Kaizen, or “continuous improvement,” which serves as the backbone for lean manufacturing . Kaizen uses the Plan, Do, Check, Act (PDCA) problem-solving cycle to encourage manufacturers to use small ideas to solve big problems, such as costly, time-intensive changeovers.
These methodologies are the building blocks of Toyota Kata , an innovative, lean way of thinking described in the book by Mike Rother, “Toyota Kata: Managing People for Improvement, Adaptiveness and Superior Results.”
In essence, Toyota Kata goes beyond problem-solving to teach management, engineers, and operators a new mindset to develop their creative and scientific-thinking skills to make them more effective, lean manufacturers. This approach looks at lean manufacturing as a culture, rather than a single process.
With the world of manufacturing evolving at a breathtaking pace thanks to developments such as Artificial Intelligence (AI), labor skill gaps, and the Industrial Internet of Things (IIoT) , Toyota Kata gives smaller manufacturers a lean strategy to help them grow with these developments. It empowers employees with the skills they can use to continuously improve, adapt, and generate ideas for a strategic, competitive advantage.
Small Steps Lead to Big Results for Manufacturers
Toyota is known as the most successful early adopter of Kaizen and the originator of the “continuous improvement” philosophy for manufacturers as part of its innovative Toyota Production System . This approach helped the company create vehicles famous for their reliability, while eliminating production waste, time, and energy resources. Toyota’s “plan slowly and act quickly” philosophy helped create the Prius hybrid, which positioned the company as the leader in hybrid technology. More than 80 years after the company’s founding, Toyota is the world’s largest automaker .
Toyota Kata builds on Toyota’s “continuous improvement” success model, so other manufacturers can learn from its example. This approach has become increasingly popular with manufacturers who want to move beyond short-term production goals to empower their workforce to implement daily, sustainable process improvements.
In Arkansas, Almatis Premiun Alumina had previous experience working with lean tools and using those tools in the traditional point solutions approach that led to obvious improvements and positive results. The challenge was to sustain continuous improvement. The company was interested in revitalizing its lean efforts and pursuing sustainability. Almatis contacted the Arkansas Economic Development Commission – Manufacturing Solutions (AEDC-MS), the MEP Center in Arkansas, for assistance.
AEDC-MS sought to create a program that would target bottom-line improvements through process cost reductions. A team of 18 people identified, managed and capitalized on opportunities within the manufacturing process. AEDC-MS led eight hours of Lean 101 training, including introductions to the Improvement Kata. Then, the team used leadership coaching to focus on individual responsibilities, human nature’s tendency to oppose change and exposure to the scientific process of continuous improvement. Sixteen hours of Value Stream Mapping was used to address the needs of a specific manufacturing line and office activities. Extra time was spent with the Almatis management team to assure they were ready for Kata delivery. A three-day Toyota Kata session led to a $12,000/month savings in the first two days of implementation, providing a full return on investment within the first 30 days of improvement.
Other results achieved included:
- $2.5M in increased or retained sales over one year
- 160 new or retained jobs
- $200,000 in cost savings
- $475,000 in new investment
How to Integrate Toyota Kata Within Your Facility
To help small and medium-sized manufacturers achieve lean success like Almatis and Toyota, the MEP National Network TM has developed a Toyota Kata overview: Toyota Kata: Developing the Skills to Thrive in Today’s Constantly Changing Marketplace .
This overview highlights that, while smaller manufacturers may not have the level of strategic resources like the behemoth Toyota, they can apply the same methodologies of Toyota Kata, including:
- Developing new habits and allowing people to think differently about problems and goals
- A way of working, and of working together
- Using scientific thinking as an ingredient to make teams and organizations more effective and successful
- Developing a culture of continuous learning and improvement at all levels through deliberate practice
Implementation of Toyota Kata begins with the aptly-named Starter Kata. Starter Kata focuses on small protocols and processes that, when practiced early and often, help manufacturing employees learn faster and teaches them to work more collaboratively. The two main elements of Starter Kata are Improvement Kata and Coaching Kata, as noted in the above Almatis example.
The Improvement and Coaching Kata help employees:
- Understand the direction or challenge
- Grasp the current condition
- Establish the next target condition
- Experiment toward the target condition
By integrating Toyota Kata as part of your manufacturing best practices, your employees can successfully overcome obstacles and develop more confidence and scientific thinking to solve problems.
The MEP National Network’s overview of Toyota Kata is a first step to empowering your workforce to become more agile, so they can find new ways to cut waste, develop new technologies, and adapt to these new changes in the ever-increasing competitive world of manufacturing.
About the author
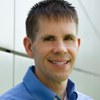
Brian Lagas
Brian Lagas manages NIST MEP's Continuous Improvement, Toyota Kata, Sustainability and Export initiatives.
Related posts
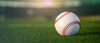
If You Build It, They Will Come – Opening Day Musings From a Baseball Fan
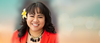
Rachel Camarillo: Blazing a Trail for Women in Manufacturing
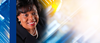
When a Friendly Check-In Call Changes Your Career Path
Add new comment.
- No HTML tags allowed.
- Web page addresses and email addresses turn into links automatically.
- Lines and paragraphs break automatically.
The Lean Post / Articles / How the Toyota Way and Toyota Kata Fit Together
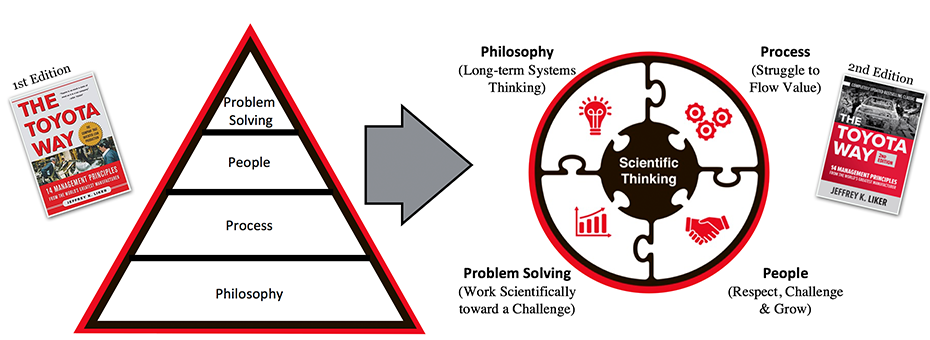
Executive Leadership
How the Toyota Way and Toyota Kata Fit Together
By Jeffrey Liker
March 18, 2022
The author of The Toyota Way explains where Toyota Kata fits with Toyota’s broader management principles — and how each enhances the other to help you build more effective organizations.
Recently, I’ve noticed some confusion about the relationship between the Toyota Way and Toyota Kata . So, with the publication of the second edition of my book, The Toyota Way , I want to clarify the differences.
The Toyota Way and Toyota Kata are management concepts described in well-known books that reveal the thinking and practices underlying the company’s success. The Toyota Way summarizes the management system Toyota has evolved over the last century as a set of fourteen principles. Toyota Kata describes the practice routines Mike Rother developed to aid people in getting started developing the habit of scientific thinking he saw as central to Toyota’s success.
The term “scientific thinking” can be confusing and might spark the picture of a lone scientist sitting in the lab conducting some fundamental research and developing abstract models. However, in lean management and problem-solving, scientific thinking refers to the mindset and practices that enable people to achieve challenging goals. In teaching and coaching scientific thinking, lean practitioners, then, are trying to develop people’s “practical scientific thinking” skills, which will help enhance their problem-solving capabilities.
These were written about in different books and are often practiced as though they are different schools of thought or approaches to lean transformation. So the question is: Are these two systems compatible, or do we have to choose to believe in one or the other?
I have had an insider seat to both since I have been studying Toyota for about 40 years, and Mike was my graduate student at the University of Michigan and lives close by. So we regularly have long discussions about these topics.
My overall conclusion is that while I was deriving general management principles from my learning about Toyota, Mike was delving into a practical approach to one of the core aspects — problem-solving through scientific thinking.
Mike’s model of scientific thinking — the Improvement Kata Pattern — was derived from watching some of the best Toyota Production System (TPS) masters in Toyota at work . He then went beyond the conceptual model to help others learn how to do this themselves through an age-old approach to mastering complex skills — deliberate practice with a coach!
Integrating The Toyota Way and Toyota Kata
Based on my long discussions with Mike and some soul-searching myself as to where this all fits together, I changed the foundational 4P model of The Toyota Way to place scientific thinking in the center ( see illustration below ).
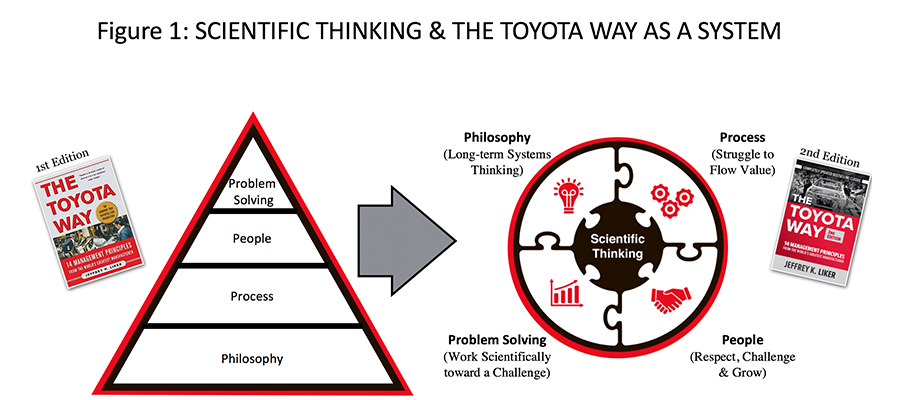
In the first edition published in 2004, I had represented the model as a pyramid, placing philosophy as the foundation and problem-solving at the pinnacle. At that time, it had seemed that scientific thinking should be a part of problem-solving. However, after thinking more about it, I made two significant changes to the model for the 2020 second edition:
- I changed the model to a set of interconnected puzzle pieces to show that all the components are interrelated — a system.
- I put scientific thinking at the system’s center after concluding that all the principles are more effective with a scientific approach. For example, though the process principles seem to lead to a straightforward implementation of tools, like a work cell , they don’t. Instead, with a scientific approach, you start with a vision or objective, such as achieving one-piece flow of value to customers. You then experiment with ways to work toward this vision, continually learning and refining your process .
Seeing Scientific Thinking in the TPS
While “scientific thinking” may seem new and perhaps theoretical, it is consistent with Toyota’s teachings, going back to the first TPS manual by Taiichi Ohno: “On the shop floor, it is important to start with the actual phenomenon and search for the root cause in order to solve the problem. In other words, we must emphasize getting the facts.”
One of Ohno’s students, Hajime Ohba, later explained in a public presentation: “TPS is built on the scientific way of thinking … How do I respond to this problem? Not a toolbox. [You have to be] willing to start small, learn through trial and error.”
In his excellent 2004 Harvard Business Review article on “ Learning to Lead at Toyota ,” Steven Spear discusses the rigor with which Toyota trains all its managers to be scientific thinkers: “Trainees watch employees work and machines operate, looking for visible problems… Learners articulate their hypotheses about changes’ potential impact, then use experiments to test their hypotheses. They explain gaps between predicted and actual results… Supervisors act as coaches, not problem solvers. They teach trainees to observe and experiment.”
Compare this with Rother’s description of the basics of practical scientific thinking for the rest of us who are not PhD scientists:
- Acknowledging that our comprehension is always incomplete and possibly wrong.
- Assuming that answers will be found by testing rather than just deliberation.
- Appreciating that differences between what we predict will happen and what actually happens can be a useful source of learning and corrective adjustment.
Developing the Kata
Mike wanted to go beyond elucidating principles of scientific thinking, so he arrived at the approach of daily practice via kata . Kata in Japanese martial arts like karate are specific movements that the master teaches to the learner through demonstration and then watching the learner try, repeatedly, until the student achieves some level of mastery of that specific, building-block skill. This approach then leads to mastering the next kata, and next, and so on. Over time, the karate student moves from practicing individual kata to combining them as situationally demanded when fighting. Those who have seen The Karate Kid have seen kata in practice ; those who have watched a jazz band play have seen the results.
Those who have seen The Karate Kid have seen kata in practice; those who have watched a jazz band play have seen the results.
Mike provided us with the Improvement Kata and Coaching Kata — including a set of practice routines, or “Starter Kata,” for each stage of the model, which people can use to practice scientific thinking deliberately.
Having a way to practice scientific thinking is critical to counter our natural “problem-solving” instincts. All of our skills and ways of thinking occur in our brains. Routine actions like maneuvering our car are bundles of connected neurons that we can call up, somewhat like computers call up subroutines. However, the problem is our natural subroutines for solving problems program us to quickly imagine solutions before deliberately thinking through the problem definition and understanding the current condition.
The Lean Community has offered various methods to prevent this jumping-to-conclusions instinct, such as systematically stepping through the plan-do-check-act ( PDCA ) process. However, neither telling people to do this nor several-day problem-solving workshops are enough to create new, counter-intuitive neural circuits.
It is tempting to try to devise a way to flush our minds clean of these old thinking habits, but what is in our brain does not in any natural way get wiped as we can do to a computer’s memory. Instead, we must build new neurological structures that, when strengthened through practice, become our go-to for addressing problems. The old well-worn ways of fast thinking start to fade into the background since we do not use them, and the new slow-thinking patterns start feeling more natural. We are practicing, or should I say “deliberately practicing,” a new way and in doing so rewiring our brains.
Creating Daily Habits of Deliberate Practice
Toyota teaches practical scientific thinking to each manager, beginning when they are hired, and coaches reinforce the practice daily. But the rest of us need some regimen to practice deliberately. Mike’s Improvement Kata serves this purpose ( See illustration below ).
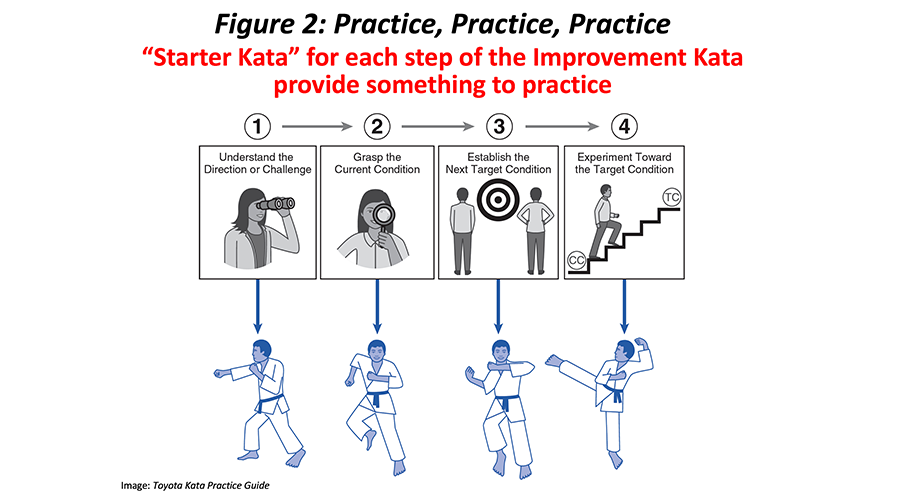
In total, the Improvement Kata starts with a clear purpose in the form of a measurable challenge, and then we iteratively learn our way to the challenge. The starting assumption is that we do not know how to meet the challenge because of too much uncertainty. So we have to step our way through it experiment by experiment, adjusting and learning as we go. Most people are uncomfortable not knowing, accepting uncertainty, and recognizing that the future is not predictable. Therefore, we need to practice our reactions when confronted with such situations, ideally with a coach.
The emphasis in Toyota is on learning by doing . Toyota values theory, but as a basis for developing practice through experimenting.
Now, we all know the emphasis in Toyota is on learning by doing. Toyota values theory but only as a basis for developing practice through experimenting. To make this scientific-thinking pattern gel in our minds, we need enough practice to create strong neural pathways.
Understanding the Neuroscience of Learning
We also know that there is a limit to how much new input our brains can absorb in one session, and it’s less than you might think. Twenty minutes seems to be about right. Practicing for short periods daily for several months is much more impactful than morning-to-night sessions that we might have in an executive immersion training course or a one-week kaizen event.
Neuroscientists have demonstrated that behavior and thinking are interconnected (s ee illustration below ). When we do something, that information gets encoded as a bundle of neurons and synapses that connect the neurons. When we practice a particular way, we get a very efficient circuit that becomes our habit. So, for example, if we approach a problem through fast thinking, jumping to conclusions, we are more likely to address issues. To counter that tendency, we need to behave scientifically repeatedly, which will change how we think and make us more likely to approach problems that way in the future.
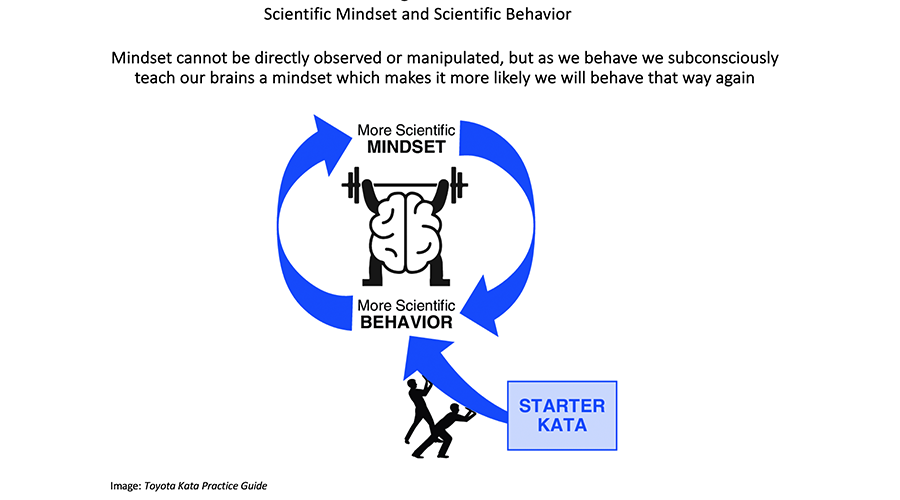
When you put this all together, you get the Improvement Kata model and its associated practice routines done in a coach-learner relationship. Toyota seems to do it naturally without a lot or scripting of how the coach teaches the student. Mike has made it explicit and more structured in Toyota Kata to help those who are not already in a mature organization with a culture of scientific thinking.
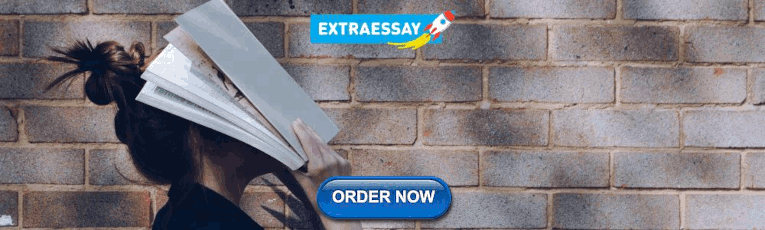
Does Toyota Kata Replace the Toyota Way?
Does this mean that Toyota Kata now replaces the Toyota Way since scientific thinking is at the center? Certainly not. The 4Ps of the Toyota way reflect a management system that is more than individual people thinking scientifically. It starts with a collective clarity of purpose and core values that guide the overall enterprise. What is the organization’s purpose? What is the collective vision for how we want the enterprise to operate? This system must be lived and modeled by all managers to become the guiding force of the culture.
The Toyota Way starts with a collective clarity of purpose and core values that guide the overall enterprise.
Philosophy does not emerge from experiments but needs to be carefully thought through and embraced to help provide direction to specific improvement efforts. Similarly for Process, there is a body of knowledge about lean processes and moving toward one-piece flow that you are not likely to discover through experimentation within a mass-production system. As a result, we need to develop people’s capabilities in many ways besides scientific thinking to get to the leadership and culture we desire. Problem-solving is best done with a scientific mindset and includes ways to align goals ( hoshin kanri ) toward a clear strategy for the products and services of the firm.
We should also recall that Mike calls these “starter kata” rather than “finishing kata.” So, he does not intend for people learning scientific thinking to continue forever to follow the “starter kata” precisely as if it were a new rigid method for problem-solving. Instead, they are for the student to practice — and develop — a scientific thinking mindset. Perhaps we can view the kata as a catalyst that juices scientific thinking, which, in turn, is the engine that drives the Toyota Way. Without it, or some equivalent way of developing people to think scientifically, the Toyota Way might remain at the level of principles without practice.
Editor’s Note: In case you missed it! This Lean Post is a lightly edited version of an article published in February 2021.
Improvement Kata/Coaching Kata
Develop Scientific Thinking, a Foundation of Lean Management in the 21st Century.
Written by:
About Jeffrey Liker
Dr. Jeffrey K. Liker is Professor of Industrial and Operations Engineering at the University of Michigan, owner of Liker Lean Advisors, LLC, Partner in The Toyota Way Academy, and Partner in Lean Leadership Institute. Dr. Liker has authored or co-authored over 75 articles and book chapters and eleven books.
He is author of the international best-seller, The Toyota Way: 14 Management Principles from the World’s Greatest Manufacturer , McGraw-Hill, 2004 which speaks to the underlying philosophy and principles that drive Toyota’s quality and efficiency-obsessed culture. The companion (with David Meier) The Toyota Way Fieldbook , McGraw Hill, 2005 details how companies can learn from the Toyota Way principles. His book with Jim Morgan, The Toyota Product Development System , Productivity Press, 2006, is the first that details the product development side of Toyota. Additional books in The Toyota Way Series are (with David Meier), Toyota Talent: Developing exceptional people the Toyota Way (May, 2007), (with Michael Hoseus) Toyota Culture: The Heart and Soul of the Toyota Way (January, 2008), (with Gary Convis) The Toyota Way to Lean Leadership (2012), (with James Franz) The Toyota Way to Continuous Improvement (2012), (with Tim Ogden) Toyota Under Fire (2012), and (with George Trachilis) Developing Lean Leaders The Toyota Way (2014). His articles and books have won eleven Shingo Prizes for Research Excellence and The Toyota Way also won the 2005 Institute of Industrial Engineers Book of the Year Award and 2007 Sloan Industry Studies Book of the Year.
In 2012 he was inducted into the Association of Manufacturing Excellence Hall of Fame. He is a frequent keynote speaker and consultant. Recent clients include Caterpillar, Applied Materials, Siemens, Dover Industries, Kraft-Oscar Meyer, Alcatel-Lucent, Hertz, Solar Turbine, Art Van Furniture, and Henry Ford Health Systems.
Leave a Comment Cancel reply
Your email address will not be published. Required fields are marked *
Save my name, email, and website in this browser for the next time I comment.
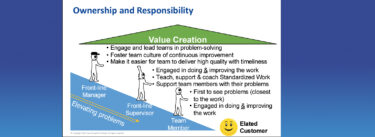
What Matters When Giving — or Accepting — the Gift of Lean Thinking and Practice
Article by Josh Howell
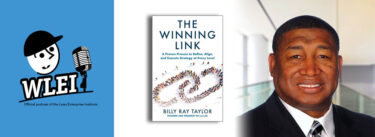
Defining Winning: Turning Around Operations Through Clarity and Ownership with Billy Taylor
Podcast by Matthew Savas
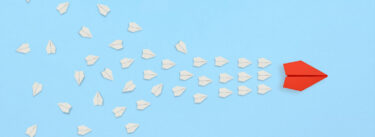
Are You Organized for Leadership?
Related books
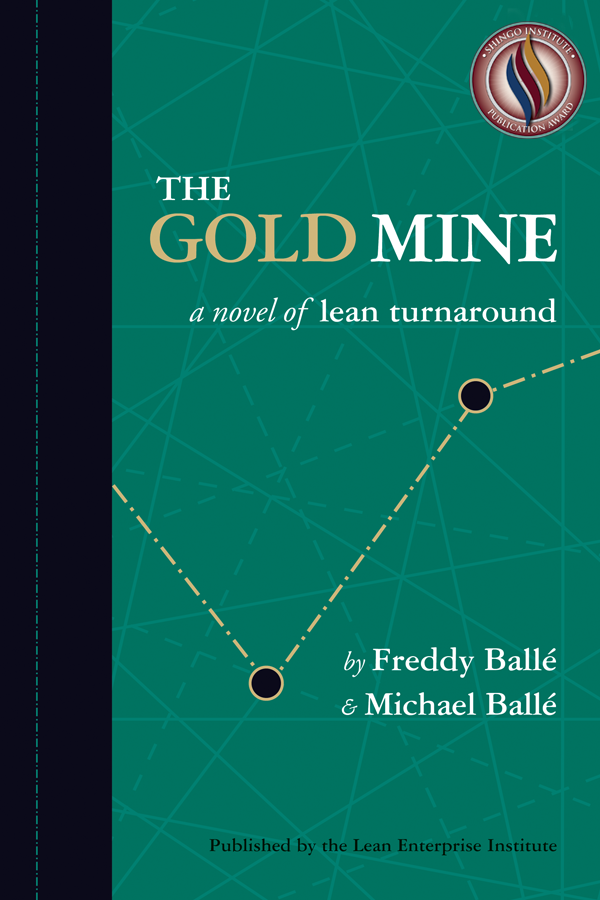
The Gold Mine (Audio CD)
by Freddy Ballé and Michael Ballé
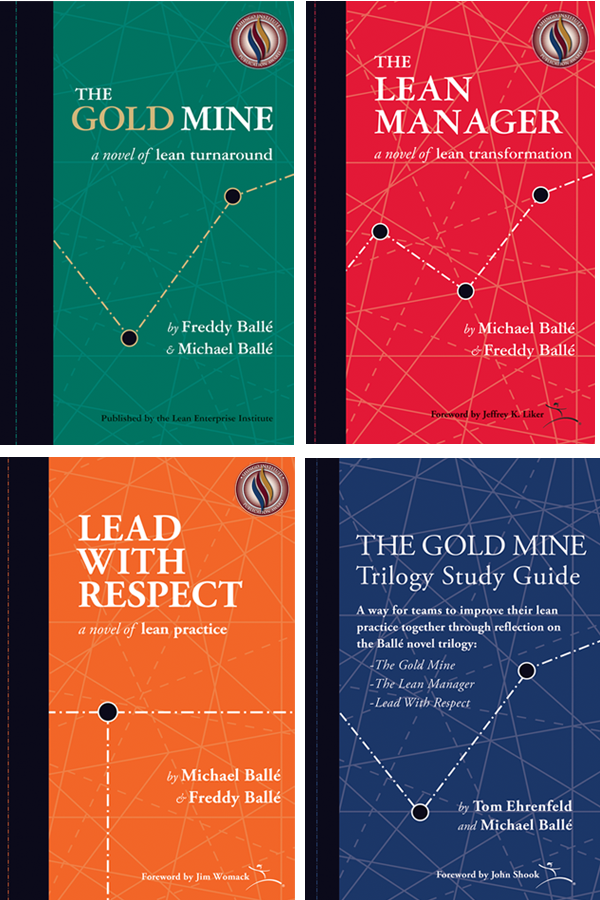
The Gold Mine Trilogy 4 Book Set
Related events
April 04, 2024 | Coach-Led Online Course
Executing Strategy
April 08, 2024 | Coach-Led Online Course
Managing to Learn
Explore topics.
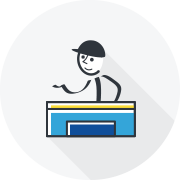
Subscribe to get the very best of lean thinking delivered right to your inbox
Privacy overview.
The Lean Thinker
Thoughts and Insights from the Shop Floor
Toyota Kata “A3 Problem Solving”
Over the years, I’ve been exposed a number of efforts to “implement A3 problem solving” in various companies. I worked for some of those companies, I’ve observed others.
The results are nearly always the same.
Here are a couple of examples. Let me know if any of these match up with experiences you have had.
Example 1: The company had put many people through “Practical Problem Solving” training and was (ironically) trying to measure how many problem solving efforts were underway.
I was watching a presentation by one of these problem solving teams to management. Their A3 was on a computer, projected onto the screen. They were reporting their “results.” Yet there were large discontinuities in their problem solving flow. The actions they were taking simply did not link back (through any kind of identifiable cause) to the problem they were solving.
The management team listened carefully, applauded their efforts, and moved on to the next topic of their meeting.
Example 2: A different company had a form to fill out called an “MBF” or “Management by Fact.” From the labels on the boxes, it was clearly intended to be structured problem solving. By the time I worked there, however, “MBF” had become a verb. It was a solo activity, filling out the form at the desk, and reporting on it in a staff meeting.
Example 3: Well-meaning former Toyota team members, now working for a different large company wanted to “train everyone in problem solving.” They put together a “class” that presented the purpose of each block on their A3 form with the expectation that people would adopt the process.
All of these efforts had something in common.
They didn’t work.
Over the last few days, I’ve been privileged to be included in an email exchange about the relationship between A3 and Mike Rother’s Toyota Kata . My small contribution was apparently enough to get my name onto the cover, but I want to give a real nod in the direction of a Jenny Snow-Boscolo for instigating inspiring a really good exchange.
One of the difficulties with gaining insight into Toyota’s management processes is that they really aren’t codified. This shouldn’t be a surprise. Look at your own company, and ask how much of the culture – the reflexive way things are done and interactions are structured – is written down.
(In fact, if it is written down, I would contend it is likely your actual culture has little resemblance to what is written about it. Those things tend to be more about what they wish the culture was.)
Culture, any culture, is learned through daily interaction. This is all well and good in cases where people are immersed in it from the beginning.
But the rest of us aren’t operating in that problem solving culture. Rather, we are trying to create it. And as the former Toyota Team Members from Example 3 (above) learned, it isn’t a simple matter of showing people.
Rather than two different things, we are looking at a continuum here. At one end is the culture described on Slide 9. There isn’t any formal structure to it, the process for teaching it isn’t codified. It is learned the same way you learn the way to get the job done in any company. They just learn different things than you did.
But in another organization there is no immersion. If there is anyone who is steeped in The Way, they are few and far between.
In these cases, we want to start with something more overt. And that is the purpose of having a rote drill or kata . It isn’t something you implement. It is a structure, or scaffold, to learn the basic moves. Just as mastering the musical scales is only a prelude to learning to play the instrument, the kata is the foundational structure for learning to apply the underlying thinking patterns.
Share this:
2 replies to “toyota kata “a3 problem solving””.
You failed to mention that many of us called “Management by Fact” by another name – “Management by Fiction.” While the former was the intention, the latter happened more often than the leaders knew.
“You must unlearn what you have learned.” -Yoda
Late to the post, but I came across it as I consider another foray into an A3-trained organization. Examples 1 and 3 are certainly familiar, though in my experience it was somebody far less qualified than a Toyota consultant who taught the organization that if they did A3 reports, Lean-thinking would commence (incidentally, this was at the same healthcare organization where I met you, Mark, when you contributed your time and knowledge toward using Toyota Kata in a healthcare setting, thus beginning our daily practice there. Thank you!). The result of “the A3 is the most important Lean tool” thinking was that by the time I was brought on board there were scattered yellowed-with-age A3 reports on a few department white boards and a general consensus of “we tried Lean and it didn’t really work” along with resistance to devoting any time to delving deeper into Lean management.
Unfortunately misery does not love company in this case. I would prefer that it was an isolated case, but as exemplified by the fact that you are writing about the issue, it is not. As more organization “tried Lean” this will likely become more and more common. I like the idea of incorporating the kata into A3 reporting for those managers who are already using it, but when an executive team than has “done Lean” and moved on to other projects, changing the habits of the senior leadership may be the most important obstacle that needs to be addressed for the organization to succeed; possibly through iterative experiments toward the target condition of a transformed executive team!
Leave a Reply Cancel reply
Your email address will not be published. Required fields are marked *
Notify me of follow-up comments by email.
Notify me of new posts by email.
This site uses Akismet to reduce spam. Learn how your comment data is processed .
- Contact Your Regional Manager
- News and Blogs
- Staff Portal

Toyota Kata + PIT: Serious Fun!
Redefining problem solving: a pit crew approach to business excellence.
The Kata + Pit Crew Experience
NC State University Industry Expansion Solutions collaborates with the Performance Instruction & Training facility (PIT) in Mooresville, NC to provide participants with an immersive and practical pit crew experience. You can view firsthand the fundamental need for teamwork, preparation, speed and adaptability in high-pressure, time-sensitive situations.
What to Expect
You’ll start your day with an orientation to high-performance motorsports, followed by an activity where you become a pit crew member. This is followed by the class segment, where we learn that kata is:
- Developing new habits and allowing people to think differently about problems and goals
- A way of working, and of working together
- Using scientific thinking as an ingredient to make teams and organizations more effective and successful
- Developing a culture of continuous learning and improvement at all levels through deliberate practice
The Improvement Kata helps develop fundamental skills of working like a scientist. The learner iterates or experiments toward a desired goal instead of deciding the way forward. This way of thinking and working helps people deal with uncertainty and challenges. The Coaching Kata is a routine by which the teacher or coach gives the learner procedural guidance, not solutions, helping the learner successfully overcome obstacles and develop confidence. With Toyota Kata, managers can simultaneously build their own coaching skills and their team members’ problem-solving skills.
Instructors
The lean team from NC State University Industry Expansion Solutions facilitates the lean presentations and discussions. Senior-level PIT Instruction and Training staff facilitate the motorsports presentation and activity while professional pit crew members coach the teams.
Benefits of Participating
- Learn and understand the concept of improvement kata and coaching kata to improve your business
- Behave like a pit crew under pressure, apply lean principles and observe your impact on performance
- Discover the importance of developing a culture of continuous process improvement in your organization
Upcoming Opportunity to Attend PIT Training:
Date: April 2, 2024 Time: 8 a.m. – 4:30 p.m. Location: Performance Instruction & Training (PIT) 156 Byers Creek Road Mooresville, NC 28117 United States + Google Map

Navigate Blog
- Resource Library
Recent Posts
- Women in Manufacturing: Part 3: Women in Leadership
- Women in Manufacturing: Part 2: Women in Quality and Engineering Excellence
- Women in Manufacturing: Part 1: Women in Health and Safety
919.515.2358
[email protected], quick links.
Questions? Email or call 919.515.8584 .
Questions? Email or call 919.515.5358 .
We Can Help
Regional Managers are located across the state to help you with customized onsite training programs!
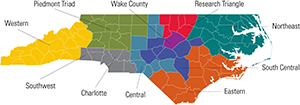
Piedmont Triad Kami Baggett 919.830.7292
Northeast Lori Benn 919.988.7475
Wake County Robert Crew 919.830.2941
Eastern Alex Easley 910.617.5650
Southwest Jennifer Fielder 704.380.0063
South Central Anna Mangum 919.210.6050
Western Chris McGraw 828.329.3119
Military - Statewide Michael Mullins 919.515.8812
Research Triangle Mitch Poteat 919.607.0684
Central Mary Tillery 910.622.5849
IES Solutions Overview
Want to quickly browse all our solutions? Click here for the complete IES Solutions Overview brochure.
- Contributors : About the Site
Newgeography.com
- Urban Issues
- Small Cities
- Demographics
Moscow, like other international urban areas , is decentralizing, despite considerable barriers. The expansion will lead to even more decentralization, which is likely to lead to less time "stuck in traffic" and more comfortable lifestyles. Let's hope that Russia's urban development policies, along with its plans to restore population growth, will lead to higher household incomes and much improved economic performance.
Wendell Cox is a Visiting Professor, Conservatoire National des Arts et Metiers, Paris and the author of “ War on the Dream: How Anti-Sprawl Policy Threatens the Quality of Life ”
Note 1: The 23 ward (ku) area of Tokyo is the geography of the former city of Tokyo, which was abolished in the 1940s. There is considerable confusion about the geography of Tokyo. For example, the 23 ward area is a part of the prefecture of Tokyo, which is also called the Tokyo Metropolis, which has led some analysts to think of it as the Tokyo metropolitan area (labor market area). In fact, the Tokyo metropolitan area, variously defined, includes, at a minimum the prefectures of Tokyo, Kanagawa, Chiba and Saitama with some municipalities in Gunma, Ibaraki and Tochigi. The metropolitan area contains nearly three times the population of the "Tokyo Metropolis."
Note 2: The expansion area (556 square miles or 1,440 square kilometers) has a current population of 250,000.
Note 3: Includes all residents in suburban districts with at least part of their population in the urban area.
Note 4: Urban area data not yet available.
Photo: St. Basil's Cathedral (all photos by author)
- Login to post comments
- Evolving Urban Form: Development Profiles of World Urban Areas
- Transportation
Comment viewing options
Road in city area.
The roads and ways of the city areas are very clumsy and many accidents are happening due to the short road. But you need to maintain the driving properly otherwise you may face accident. So now the government decided to expand the road which may put the positive effect on automobile sector. I think it is a helpful service for the society people. If you have a BMW car and you have faced any problem then better to repair it at BMW Repair Spring, TX for the best service.
Transit & transportation
Transit and transportation services are quite impressive in most of the urban cities; therefore people were getting better benefits from suitable transportation service. Urban cities like Moscow, Washington, New York and Tokyo; we have found high margin of transportation system that helps to build a better communication network in these cities. I hope through the help of modern transportation system we are able to bring revolutionary change in automobile industries; in this above article we have also found the same concepts to develop transportation system. Mercedes repair in Torrance
Moscow is bursting Noblesse
Moscow is bursting Noblesse at the seams. The core city covers more than 420 square miles (1,090 kilometers), and has a population of approximately 11.5 million people. With 27,300 residents per square mile (10,500 per square kilometer), Moscow is one percent more dense than the bleach anime watch city of New York, though Moscow covers 30 percent more land. The 23 ward area of Tokyo (see Note) is at least a third more dense, though Moscow's land area is at least half again as large as Tokyo. All three core areas rely
Belgravia Villas is a new
Belgravia Villas is a new and upcoming cluster housing located in the Ang Mo Kio area, nested right in the Ang Mo Kio landed area. It is within a short drive to Little India, Orchard and city area. With expected completion in mid 2016, it comprises of 118 units in total with 100 units of terrace and 18 units of Semi-D. belgravia villas
Russians seeing the light while Western elites are bickering?
What an extremely interesting analysis - well done, Wendell.
It is also extremely interesting that the Russian leadership is reasonably pragmatic about urban form, in contrast to the "planners" of the post-rational West.
An acquaintance recently sent me an article from "The New Yorker", re Moscow's traffic problems.
The article "abstract" is HERE (but access to the full article requires subscription)
http://www.newyorker.com/reporting/2010/08/02/100802fa_fact_gessen
One classic quote worth taking from it, is: "People will endure all manner of humiliation to keep driving".
I do find it odd that the "New Yorker" article author says nothing at all about the rail transit system Moscow had, on which everyone was obliged to travel, under Communism. It can't surely have vaporised into thin air?
Moscow is a classic illustration of just how outmoded rails are, and how important "automobility" is, when the auto supplants rails so rapidly than even when everybody did travel on rails up to a certain date, and the road network dates to that era, when nobody was allowed to own a car; an article written just 2 decades later does not even mention the rail transit system, other than to criticise the mayor for "failing to invest in a transit system".......!!!!!!!!
This is also a give-away of "The New Yorker's" inability to shake off the modern PC ideology on rails vs cars.
Subscribe to NG Articles
Get new posts by email:, connect with us:.

NewGeography.com is a joint venture of Joel Kotkin and Praxis Strategy Group
Featured Content
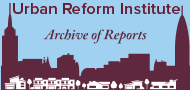
The Coming of Neo-Feudalism

Infinite Suburbia
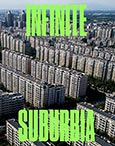
Recent blog posts
- Shift of Net Domestic Migration to Smaller MSAs and Outside CBSAs
- Feudal Future Podcast: Navigating the Global Politics That May Shape America's 2024 Elections
- YIMBY Can Populate Conference Halls (at Least)
- Feudal Future Podcast: Exploring the Impact of Catholic Schools on Underserved Communities
- Feudal Future Podcast: Exploring the Paradox of Peace and Economics in Taiwan-China Relations
- Feudal Future Podcast: Navigating the Future of Higher Education
- U.S. Tallest Building Set for Oklahoma City?
- Goodbye to Davos and Good Riddance
- Largest San Francisco Shopping Center Sheds Value, Tenants
- Shaving Time Off Suffolk County Homebuilding
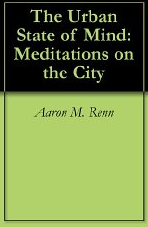
Recent popular content
- California's Electricity Disaster in Seven Charts
- Why I'm Bullish on Generation Z
- The Dispersion of Financial Sector Jobs
- Trump’s Pitch to Blacks
- California is a Bastion of Innovation Marred by Deep Inequality. Is That America's Future?
- The Evolving Urban Form: Jing-Jin-Ji (Dispersing Beijing)
- The Emerging Geography of Inequality
- If Wishes Were Iron Horses: Amtrak Gaining Airline Riders?
More from this author
- Largest World Cities: 2014
- Largest Cities in the World: 2016
- World Urban Areas Population and Density: A 2012 Update
- Largest 1,000 Cities on Earth: World Urban Areas: 2015 Edition
- The Evolving Urban Form: Rio de Janeiro
Recommended Books
Blogroll and partner sites.
- Burgh Diaspora
- Center for Economic Research and Forecasting
- China Urban Development Blog
- Chris Bradford - Austin Contrarian
- Houston Strategies
- LA Observed
- Multiplier Effect: Levy Economics Institute
- The Rural Blog
- The Urbanophile
- Request new password
- © 2024 New Geography
- CONTRIBUTORS :
- PRIVACY POLICY
- Stay up to date:

- Russian Program for Fluency course
Label Links
- To Survive in Russia
- To Learn Russian
- To Understand Russians
- The Program
- Emergencies
- Quick Notes
- Travellers' Notes
Recommended
Moscow’s life 7 biggest problems and 7 solutions.

Being sick never feels nice. Imagine asking for help in this state while being in a foreign country…You would need to strain your memory while struggling to remember any Russian words or phrases. Speaking a foreign language alone is stressful enough, add to this a state of being sick and you’ll find yourself completely frustrated. But what if you could speak Russian without stress, automatically and effortlessly? I’m not suggesting you to buy some super awesome course that will make you learn Russian in 7 days. In fact, I’m not suggesting you to buy anything at all :) I simply want to show you a few effective learning techniques that will help you overcome your language barrier. So, just let me know if you’re interested in joining the effective language learners community ;)
What do you tell a taxi driver, how do you use one of Russia’s minivan taxis and how far does a “one-ride” ticket in the metro take you? Find these great tips in our article Navigating In Russian Cities . We’ll make sure you never get lost in Russia!
If you do want to try out your luck with approaching “busy people of the capital”, you might want to consider being at least a bit prepared for it, i.e. in case you don’t want to be shoved away on the spot, you might need a few handy phrases to start off a conversation and grab local’s attention by saying something in Russian. But you should also be ready for a rather fast and at some point harsh answer. The good news is that there’s a way to be prepared for such situations. And I can show you how.
Like to share?
Current mission.
“Make you feel comfortable and confident in Russia... almost like in your hometown!"
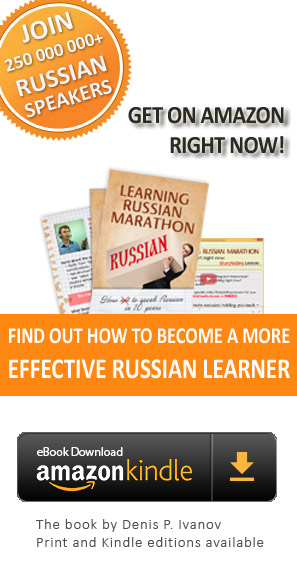
Connect With Us

Recent posts
- Amazon Book: Learning Russian Marathon
- Learning To Know Facebook
Random Posts
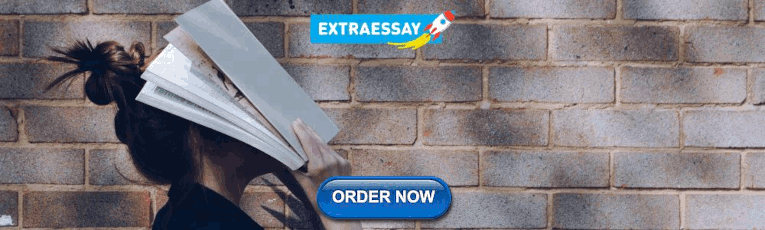
IMAGES
VIDEO
COMMENTS
Kata is Japanese for "model" and the four steps of the model are: Understand Your Direction and Set a Challenge. Grasp the Current Condition. Set the Next Target Condition. Conduct the Experiments to Get There. Improvement Kata is designed to become a teachable, daily practice that emphasizes scientific thinking and problem solving.
Toyota Kata is a methodology designed to take on Lean's biggest challenge by changing the way workers think and solve problems. Below, we'll take a look at the core elements of Toyota Kata and how it can be used to drive meaningful change through regular practice.
Toyota Kata is a problem-solving and continuous improvement method developed by Mike Rother, based on the practices and principles of Toyota Motor Corporatio...
The Improvement Kata and Coaching Kata were introduced to the lean community by Mike Rother in 2010 in his book Toyota Kata.In 2021, Dr. Jeffery Liker highlighted the practices in The Toyota Way, 2nd Edition, crediting the use of the two kata as an effective way to develop the scientific problem-solving method of PDCA and embed it in an organization's work processes.
The Toyota Kata method is a great asset for installing sustainable thinking and behavioral routines within the company to achieve the desired objectives and develop the necessary problem-solving skills. It emphasizes the importance of learning and practicing to keep improving in a constantly changing environment.
Toyota Kata is a methodology designed to confront Lean's biggest challenge by changing the way we think, learn, and solve problems. This process enforces a structured, sustainable system for developing new habits that enable continuous improvement. Gemba Academy's Toyota Kata training course begins ...
Toyota Kata. Toyota Kata helps workers think differently and solve problems. It instills a scientific way of thinking, through practice and coaching by managers, to make teams more effective at problem solving and making improvements. The approach counteracts our human tendency to jump to conclusions without testing and experimentation.
thinking. Practicing the Toyota Kata routines makes anyone and any team better at navigating uncertainty and achieving challenging goals. Toyota Kata does not teach problem solving, but rather a mindset and way of reacting that makes us more effective at problem solving. It's done by practicing " Starter Kata," which
Users can implement scientific thinking by practicing the Improvement Kata, which is one of the main elements within Toyota Kata. This Improvement Kata is a series of steps that provide a mindset for problem solving. These steps include: Understand the challenge. This is typically a large, big-picture goal that may seem or feel out of reach.
The Toyota Problem Solving Kata. A common, but flawed, strategy for problem solving involves taking on complex problems and tackling many issues simultaneously. This approach makes it difficult to understand which strategies and techniques worked and which did not, as too many changes are made simultaneously. Conversely, the Toyota problem ...
At its core, Toyota Kata is a set of practices that help individuals and teams to develop and improve their problem-solving and decision-making skills. ... The Toyota Kata methodology is designed to be used on an ongoing basis. By following this process, individuals and teams can continuously experiment and learn, improving their problem ...
In essence, Toyota Kata goes beyond problem-solving to teach management, engineers, and operators a new mindset to develop their creative and scientific-thinking skills to make them more effective, lean manufacturers. This approach looks at lean manufacturing as a culture, rather than a single process. ...
The Toyota Way and Toyota Kata are management concepts described in well-known books that reveal the thinking and practices underlying the company's success. The Toyota Way summarizes the management system Toyota has evolved over the last century as a set of fourteen principles. Toyota Kata describes the practice routines Mike Rother ...
Toyota Kata is not a problem-solving tool, but it's a methodology to become a learning organization. The Toyota Kata helps the organization to become more agile, innovative and to solve problems. It works with the mindset to increase the speed of learning. Toyota Kata is divided in two main categories: Improvement Kata and Coaching Kata.
Toyota Kata is a managerial approach that trains people to achieve continual improvement while leveraging scientific thinking. It does not teach problem-solving, but rather a mindset that can make people more effective at problem-solving. By utilizing this systematic mindset, an improvement culture can be created which will optimize gains made ...
Toyota Kata does not teach problem solving, but rather a mindset that can make people more effective at problem solving - through practicing "Starter Kata." Starter Kata are small routines or protocols that get practiced deliberately, especially at the beginning, to help people acquire a new skill. ...
Example 3: Well-meaning former Toyota team members, now working for a different large company wanted to "train everyone in problem solving.". They put together a "class" that presented the purpose of each block on their A3 form with the expectation that people would adopt the process. All of these efforts had something in common.
The Executive Advanced Problem-Solving program is based on important concepts in the Toyota Kata model. By using TRANSFORM (our supercharged Lean Agile problem- solving methodology), participants navigate their organization's Lean Agile journey using specialized tools and techniques. Toyota uses a similar methodology known as Toyota Business ...
These teams are known for their speed, precision, and collaboration, all while working under incredible pressure. Professionals can redefine their approach and achieve better results by applying these methods to business problem-solving. Toyota Kata + PIT Experience - April 2nd, 2024. Watch on. Teamwork is one key aspect of the pit crew approach.
The number of registered portal users has reached 5.3 million, with one in two Muscovites using the portal to obtain government services. Last year, users made more than 85 million requests. Work will continue to increase the number of services available in 2016 and make the provision of some types of services available only in the online format.
The Evolving Urban Form: Moscow's Auto-Oriented Expansion. by Wendell Cox 02/21/2012. Moscow is bursting at the seams. The core city covers more than 420 square miles (1,090 kilometers), and has a population of approximately 11.5 million people. With 27,300 residents per square mile (10,500 per square kilometer), Moscow is one percent more ...
No commitments. 3. Long distances. It always takes a long time to get around in a big city and Moscow is no exception. It's hard to get anywhere in less than 30 minutes here. Everything takes longer: getting to the metro, riding the escalator to the bottom, finding your destination. It can be very exhausting.
Thanks to Constantin Preobrazhensky (Moscow) for supplying info about the web site and the Stones show in Russia. Also thanks to Leonid Ulitsky, Italy, for info. Ticket information: +7-095-2349595 (for the orders) +7-095-2531033, +7-095-2531043 (for info) Email: [email protected] For more news see IORR 33 mailed out in May, 1998!